Efficient split type infrared burner of infrared stove
An infrared burner and split-type technology, which is applied in the field of household gas cookers, can solve the problems of complex processing technology, many processing steps, and high maintenance complexity, and achieve the effects of simple processing steps, beautiful structure and appearance, and solving antifouling defects
- Summary
- Abstract
- Description
- Claims
- Application Information
AI Technical Summary
Problems solved by technology
Method used
Image
Examples
Embodiment 1
[0074] like Figure 1 to Figure 8 , this embodiment provides a high-efficiency split-type infrared burner for an infrared stove, including:
[0075] The premixing part 1 and the combustion part 2, the premixing part 1 and the combustion part 2 are matched and connected,
[0076] The ejector 1-1, the first mixing chamber 1-2, the splitter plate 1-3 and the ignition probe assembly 1-4 are arranged in the premixing part 1; wherein the ejector 1-1 includes the inner ejector 1- 1-1 and outer ejector 1-1-2;
[0077] The first mixing chamber 1-2 includes the middle part of the first mixing chamber 1-2 arranged from the inside out, the first inner mixing chamber 1-2-2 and the first outer mixing chamber 1-2-1, the first mixing chamber 1 -2 The middle part is cylindrical, the first inner mixing chamber 1-2-2 and the first outer mixing chamber 1-2-1 are annular, the middle part of the first mixing chamber 1-2, the first inner mixing chamber 1-2 -2 and the first outer mixing chamber 1-...
Embodiment 2
[0092] like Figure 9 , the high-efficiency split-type infrared burner of an infrared cooker provided in this embodiment is different from Embodiment 1 in that the diverter plate 1-3 is divided into the inner diverter plate 1-3A and the outer diverter plate 1-3B, which are combined with the premixed Part 1 has an integrated structure. Specifically, the inner splitter plate 1-3A is arranged in the first inner mixing chamber 1-2-2, and the outer splitter plate 1-3B is arranged in the first outer mixing chamber 1-2-1. The structure is more Concentration, simple processing technology.
Embodiment 3
[0094] like Figure 10The difference between the high-efficiency split-type infrared burner for an infrared stove provided in this embodiment and the embodiment 1 is that the combustion part 2 is provided with a guide structure inclined upward from the inside to the outside, which can effectively guide the mixed gas evenly. The flow is distributed to each fire hole of the porous combustion radiant plate 2-2, which has the advantages of uniform combustion and reduced local high temperature.
PUM
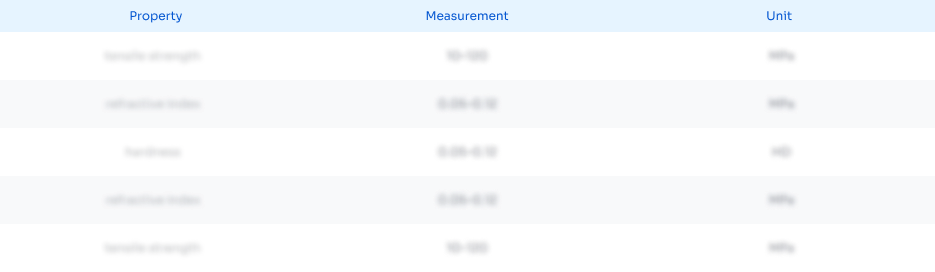
Abstract
Description
Claims
Application Information

- R&D
- Intellectual Property
- Life Sciences
- Materials
- Tech Scout
- Unparalleled Data Quality
- Higher Quality Content
- 60% Fewer Hallucinations
Browse by: Latest US Patents, China's latest patents, Technical Efficacy Thesaurus, Application Domain, Technology Topic, Popular Technical Reports.
© 2025 PatSnap. All rights reserved.Legal|Privacy policy|Modern Slavery Act Transparency Statement|Sitemap|About US| Contact US: help@patsnap.com