Cooperative robot driver based on EtherCAT, hardware FOC and gallium nitride power tube and control method
A driver and Gallium Nitride technology, applied in the direction of single motor speed/torque control, comprehensive factory control, electromechanical devices, etc., can solve problems such as the need to improve inverter efficiency, large heat generation of silicon-based power tubes, and complex program implementation , to achieve low heat generation and energy loss, stable motor operation, and board layout space saving effects
- Summary
- Abstract
- Description
- Claims
- Application Information
AI Technical Summary
Problems solved by technology
Method used
Image
Examples
Embodiment Construction
[0043] The present invention will be further elaborated and described below in conjunction with specific embodiments. The described embodiments are merely exemplary of the present disclosure and do not delineate the scope of limitation. The technical features of the various embodiments of the present invention can be combined correspondingly on the premise that there is no conflict with each other.
[0044] like figure 1 As shown, the collaborative robot driver based on EtherCAT, hardware FOC and GaN power tube provided by this embodiment includes:
[0045] The MCU microcontroller unit module is used to communicate with the host computer and other modules in the driver, configure the relevant registers of the hardware FOC module, manage the protocol stack of the EtherCAT slave module, and send and receive the sensing information of the feedback sensor module. ;
[0046] EtherCAT slave module, including EtherCAT slave chip, EEPROM and external crystal oscillator. The EtherCA...
PUM
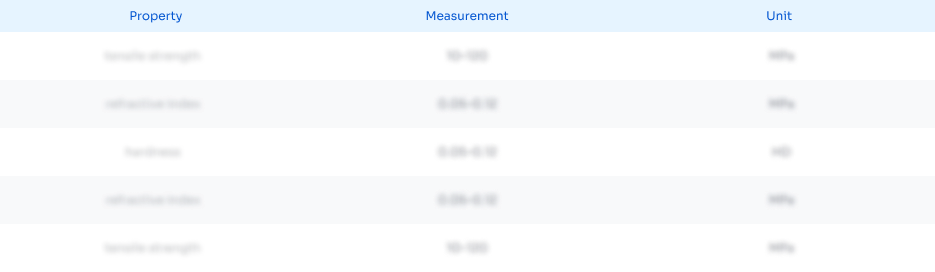
Abstract
Description
Claims
Application Information

- R&D Engineer
- R&D Manager
- IP Professional
- Industry Leading Data Capabilities
- Powerful AI technology
- Patent DNA Extraction
Browse by: Latest US Patents, China's latest patents, Technical Efficacy Thesaurus, Application Domain, Technology Topic, Popular Technical Reports.
© 2024 PatSnap. All rights reserved.Legal|Privacy policy|Modern Slavery Act Transparency Statement|Sitemap|About US| Contact US: help@patsnap.com