Method for analyzing trace hydrogen sulfide in coal gas
An analytical method and technology for hydrogen sulfide, which are applied in separation methods, chemical instruments and methods, analytical materials, etc., can solve the problems such as oxygen is not easy to undergo chemical reactions, the amount of particulate matter cannot be accurately judged, and the detection requirements cannot be met. High accuracy and sufficient gas absorption effect
- Summary
- Abstract
- Description
- Claims
- Application Information
AI Technical Summary
Problems solved by technology
Method used
Image
Examples
Embodiment 1
[0040] See Figure 1-Figure 3 , using deionized water to prepare a mixed solution of NaOH and KOH, wherein the percentage concentration of NaOH is 2%, and the percentage concentration of KOH is 2%. Take 4L as the absorption solution, and measure the H in the absorption solution 2 S concentration, denoted as W 1 , in μg / mL. At the gas production point of a steel plant, add the configured absorption liquid into the absorber tank, so that the liquid level of the absorption liquid reaches more than 1 / 2 of the height of the tank. according to figure 1 The gas inlet, suction pump I, flow meter, gas storage bag I, suction pump II, absorber, gas storage bag II, suction pump III, and gas storage bag I are connected in sequence with gas delivery pipes, respectively. Connect the absorber, the liquid volume meter, and the liquid composition analyzer in this order. Record the initial value of the flow meter, denoted as V 1 , unit L, open the air pump I, open the valve at the gas inlet...
Embodiment 2
[0047] See Figure 1-Figure 3 , using deionized water to prepare a mixed solution of NaOH and KOH, wherein the percentage concentration of NaOH is 5%, the percentage concentration of KOH is 1%, take 4L as the absorption liquid, and measure the H in the absorption liquid 2 S concentration, denoted as W 1 , in μg / mL. At the gas production point of a steel plant, add the configured absorption liquid into the absorber tank, so that the liquid level of the absorption liquid reaches more than 1 / 2 of the height of the tank. See figure 1 , the gas inlet, the gas pump I, the flow meter, the gas storage bag I, the gas pump II, the absorber, the gas storage bag II, the gas pump III, and the gas storage bag I are connected in sequence with the gas delivery pipe, and the liquid delivery pipe is used. Connect the absorber, liquid volume measuring instrument, and liquid component analysis equipment in sequence. Record the initial value of the flow meter, denoted as V 1 , unit L, open th...
Embodiment 3
[0054] See Figure 1-Figure 3 , using deionized water to prepare a mixed solution of NaOH and KOH, wherein the percentage concentration of NaOH is 3.5%, and the percentage concentration of KOH is 1.5%. Take 4L as the absorption solution, and measure the H in the absorption solution 2 S concentration, denoted as W 1 , in μg / mL. At the gas production point of a steel plant, add the prepared absorption liquid into the absorber reaction tank, so that the liquid level of the absorption liquid reaches more than 1 / 2 of the height of the tank. A three-way pipeline is placed at the gas inlet, and the gas inlet is divided into two branches, namely branch 1 and branch 2. Branch 1 adopts gas delivery pipe according to figure 1 Connect with the air pump I, and then connect the air pump I with the flow meter, the air storage bag I, the air pump II, the absorber, the air storage bag II, the air pump III, and the air storage bag I in sequence, and use the liquid delivery pipes to respectiv...
PUM
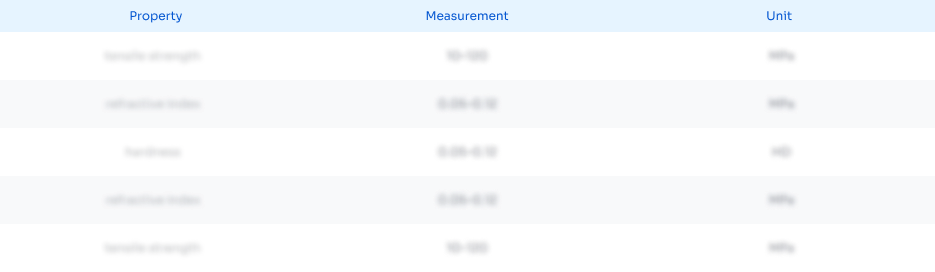
Abstract
Description
Claims
Application Information

- R&D Engineer
- R&D Manager
- IP Professional
- Industry Leading Data Capabilities
- Powerful AI technology
- Patent DNA Extraction
Browse by: Latest US Patents, China's latest patents, Technical Efficacy Thesaurus, Application Domain, Technology Topic, Popular Technical Reports.
© 2024 PatSnap. All rights reserved.Legal|Privacy policy|Modern Slavery Act Transparency Statement|Sitemap|About US| Contact US: help@patsnap.com