Corrugated web H-shaped honeycomb steel beam and manufacturing method thereof
A technology of corrugated web and manufacturing method, applied in joists, girders, trusses and other directions, can solve the structural performance limitation of honeycomb steel beams, increase the amount of steel used and the manufacturing process, and the height-to-thickness ratio of the flat web cannot be too large. and other problems, to achieve the effect of material saving, high bearing capacity, high out-of-plane stiffness and shear buckling bearing capacity
- Summary
- Abstract
- Description
- Claims
- Application Information
AI Technical Summary
Problems solved by technology
Method used
Image
Examples
Embodiment 1
[0044] Example 1: as Figure 1 to Figure 3 As shown in the figure, the corrugated web H-type honeycomb steel beam in this embodiment is a rectangular hole type corrugated web H-type honeycomb steel beam, which is composed of a corrugated web and upper and lower flange plates, wherein the corrugated web is welded on the Between the upper and lower flange plates, a plurality of rectangular openings are arranged on the corrugated web, the holes of the plurality of rectangular openings are the same and are arranged at equal intervals, and the cross section of the corrugated web is regular corrugated.
[0045] like figure 1 As shown in the figure, the processing of the H-shaped honeycomb steel beam with the rectangular hole type corrugated web includes the following steps:
[0046] 1) The flat plate is continuously molded to form a corrugated web by molding equipment;
[0047] 2) Cut the corrugated web along the set cutting path, so that the corrugated web is divided into several...
Embodiment 2
[0063] Embodiment 2: as Figures 6 to 8 As shown, the difference between this embodiment and the first embodiment is that the shape of the openings on the corrugated web is hexagonal. At this time, by calculating and planning the forming and dividing paths, each dividing unit forms a half of a hexagon, and then welding is carried out with reference to the corresponding welding method of the first embodiment, that is, the first cutting unit 1 and the second cutting unit 4 are welded, The second cutting unit 2 and the third cutting unit 3 are welded.
Embodiment 3
[0064] Example three: as Figure 9 to Figure 11 As shown, the difference between this embodiment and the second embodiment is that the sizes of the hexagonal openings on the corrugated web are different, and the difference is also realized by calculating and planning the forming and dividing paths. .
PUM
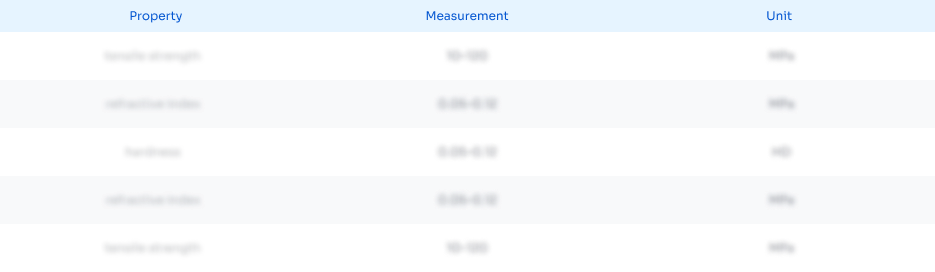
Abstract
Description
Claims
Application Information

- Generate Ideas
- Intellectual Property
- Life Sciences
- Materials
- Tech Scout
- Unparalleled Data Quality
- Higher Quality Content
- 60% Fewer Hallucinations
Browse by: Latest US Patents, China's latest patents, Technical Efficacy Thesaurus, Application Domain, Technology Topic, Popular Technical Reports.
© 2025 PatSnap. All rights reserved.Legal|Privacy policy|Modern Slavery Act Transparency Statement|Sitemap|About US| Contact US: help@patsnap.com