Preparation method for metal injection molding of SMT (Surface Mount Technology) carrier plate jig
An injection molding and carrier board technology, which is applied in the field of metal powder injection molding SMT carrier board fixtures, can solve problems such as deformation, uneven size shrinkage, cracking, etc., and achieve the effects of reducing costs, reducing imperfections, and reducing pores
- Summary
- Abstract
- Description
- Claims
- Application Information
AI Technical Summary
Problems solved by technology
Method used
Image
Examples
Embodiment 1
[0043] A preparation method for metal injection molding of SMT carrier jig, characterized in that it comprises the following steps:
[0044] 1) Mold preparation steps: According to the product drawing, all the edges without chamfering in the mold are chamfered to C0.2-C0.5, and then increase 0.2mm where the thickness of the glue position in the mold is less than 1.0mm. Thickness allowance. This can effectively avoid the bending phenomenon caused by the small local thickness of the injected embryo.
[0045]2) Prepare metal powder: select SUS301 alloy powder, in which the gas atomized SUS301 alloy powder and the water atomized SUS301 alloy powder are mixed uniformly according to the mass fraction of 5:5 and then used. Among them, the elements contained in the gas and water atomized SUS301 alloy powder are the same as the following elements by mass percentage: C0.1%, Cr18.0%, Ni6.0%, Si1.0%, Mn0.47%, S0.3%, P0.025, oxygen content PPM is 0.03%, and the balance is Fe. The partic...
Embodiment 2
[0068] The difference between Examples 2 and 1 is that the elements contained in the SUS301 alloy powder are the same as the following elements by mass percentage: C0.15%, Cr16.0%, Ni8.0%, Si0.52%%, Mn2. 0%, S0.0005%, P0.025%, oxygen content PPM is 0%, and the balance is Fe. The particle size distribution of these alloy powders was D10: 2.0 μm, D50: 9.5 μm, and D90: 21.0 μm. The degreasing temperature was 127°C, and the degreasing time was 15 hours.
Embodiment 3
[0070] The difference between Examples 3 and 1 is that the elements contained in the SUS301 alloy powder are the same as the following elements by mass percentage: C0.11%, Cr17.0%, Ni7.0%, Si0.62%%, Mn0. 5%, S0.001%, P0.035%, oxygen content PPM is 0.03%, and the balance is Fe. The particle size distribution of these alloy powders was D10: 2.0 μm, D50: 9.5 μm, and D90: 20.0 μm. The degreasing temperature was 113°C, and the degreasing time was 16 hours.
[0071] like figure 1 As shown, a metal injection molding SMT carrier board fixture 12 produced in Examples 1-3 is used, which includes a board body 12a, and a group of connector mounting holes 12b distributed in an array are evenly distributed on the board body 12a, and A group of magnet mounting holes 12c, a part of which are distributed in the array of connector mounting holes 12b, and the other part of the magnet mounting holes 12c are distributed along the length and width of the board 1, in the array of connector mountin...
PUM
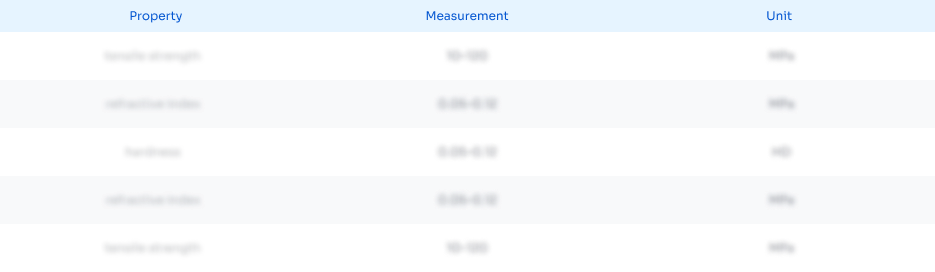
Abstract
Description
Claims
Application Information

- R&D
- Intellectual Property
- Life Sciences
- Materials
- Tech Scout
- Unparalleled Data Quality
- Higher Quality Content
- 60% Fewer Hallucinations
Browse by: Latest US Patents, China's latest patents, Technical Efficacy Thesaurus, Application Domain, Technology Topic, Popular Technical Reports.
© 2025 PatSnap. All rights reserved.Legal|Privacy policy|Modern Slavery Act Transparency Statement|Sitemap|About US| Contact US: help@patsnap.com