Thermal power plant boiler system and steam turbine power generation system with same
A technology for power generation systems and thermal power plants, which is applied in steam generation, steam engine installations, steam generation installations, etc., can solve the problem of high coupling between boiler waste heat recovery system and boiler and cannot be applied to boiler system, etc., and achieve the effect of low coupling degree.
- Summary
- Abstract
- Description
- Claims
- Application Information
AI Technical Summary
Problems solved by technology
Method used
Image
Examples
Embodiment 1
[0030] like figure 1 Shown is a boiler system of a thermal power plant provided in this embodiment, including: a boiler body 1 and a waste heat recovery circulation pipeline for recovering waste heat in high temperature flue gas in the boiler body 1 .
[0031] An evaporator 7 is installed in the tail flue of the boiler body 1. The high temperature flue gas enters the furnace and exchanges heat with the evaporator 7. A pulverized coal inlet 15 is provided on the side wall of the furnace for adding pulverized coal to the boiler body 1 for combustion. A superheater group, a reheater group, an air preheater 8 and a dust collector 9 are also installed in the furnace chamber of the boiler body 1. The evaporator 7 is arranged between the air preheater 8 and the dust collector 9. The air preheater 8 The air inlet 17 is communicated with the upper part. The evaporator 7 is made of corrosion-resistant and wear-resistant materials such as corrosion-resistant low-alloy carbon steel, comp...
Embodiment 2
[0036] This embodiment provides a steam turbine power generation system, including the thermal power plant boiler system described in Embodiment 1. It also includes a high-pressure cylinder, a medium-pressure cylinder and a low-pressure cylinder that are coaxially connected. The steam-side output end of the low-pressure cylinder is sequentially installed with a condenser, a condensate pump, a low-pressure heater, a deaerator, a feed pump and a high-pressure heater. The water output by the boiler is input to the boiler body 1 of the boiler system of the thermal power plant for heating, and then input to the high-pressure cylinder and the medium-pressure cylinder to complete the cycle. The steam-side outlet end of the final-stage superheater 2 is communicated with the high-pressure cylinder, and the steam-side outlet end of the final-stage reheater 3 is communicated with the medium-pressure cylinder.
[0037] A circulating cooling branch is communicated between the condenser and...
PUM
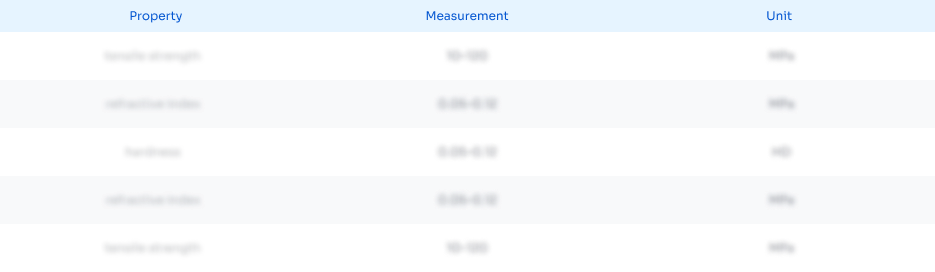
Abstract
Description
Claims
Application Information

- Generate Ideas
- Intellectual Property
- Life Sciences
- Materials
- Tech Scout
- Unparalleled Data Quality
- Higher Quality Content
- 60% Fewer Hallucinations
Browse by: Latest US Patents, China's latest patents, Technical Efficacy Thesaurus, Application Domain, Technology Topic, Popular Technical Reports.
© 2025 PatSnap. All rights reserved.Legal|Privacy policy|Modern Slavery Act Transparency Statement|Sitemap|About US| Contact US: help@patsnap.com