Preparation and application of graphite phase carbon nitride nanosheet loaded silver monatomic photocatalyst
A graphite-phase carbon nitride and photocatalyst technology, which is applied in the field of photocatalytic materials, can solve problems such as photogenerated carrier recombination, and achieve cost-saving effects
- Summary
- Abstract
- Description
- Claims
- Application Information
AI Technical Summary
Problems solved by technology
Method used
Image
Examples
Embodiment 1
[0042] a. Put 15g of urea into an alumina crucible, heat up to 550°C with a heating rate of 2°C / min in a muffle furnace, and then cool to room temperature, then heat up to 550°C with a heating rate of 5°C / min Carry out calcination, and finally, after it is lowered to room temperature, the temperature is raised to 550° C. at a heating rate of 2° C. / min for calcination to obtain a pale yellow solid powder material, which is ground evenly and used for later use.
[0043] b. Take 0.1 g of the light yellow solid powder material obtained in step a and place it in 30 mL of deionized water, and stir fully to obtain a uniformly dispersed g-C 3 N 4 / water mixed solution;
[0044] c. Add 0.10 mL of AgNO with a concentration of 1 mg / mL dropwise 3 solution, so that the Ag loading is controlled at 0.48% (mass fraction);
[0045] d, adding AgNO in step c 3 g-C 3 N 4 / Water mixed solution is ultrasonically treated, and a uniform pale yellow suspension is obtained after ultrasonication f...
Embodiment 2
[0050] a. Put 15g of urea into an alumina crucible, heat up to 550°C with a heating rate of 2°C / min in a muffle furnace, and then cool to room temperature, then heat up to 550°C with a heating rate of 5°C / min Carry out calcination, and finally, after it is lowered to room temperature, the temperature is raised to 550° C. at a heating rate of 2° C. / min for calcination to obtain a pale yellow solid powder material, which is ground evenly and used for later use.
[0051] b. Take 0.1 g of the light yellow solid powder material obtained in step a and place it in 30 mL of deionized water, and stir fully to obtain a uniformly dispersed g-C 3 N 4 / water mixed solution;
[0052] c. Add 0.25mL of AgNO with a concentration of 1mg / mL dropwise 3 solution, so that the Ag loading is controlled at 0.87% (mass fraction);
[0053] d, adding AgNO in step c 3 g-C 3 N 4 / Water mixed solution is ultrasonically treated, and a uniform pale yellow suspension is obtained after ultrasonication for...
Embodiment 3
[0058] a. Put 15g of urea into an alumina crucible, heat up to 550°C with a heating rate of 2°C / min in a muffle furnace, and then cool to room temperature, then heat up to 550°C with a heating rate of 5°C / min Carry out calcination, and finally, after it is lowered to room temperature, the temperature is raised to 550° C. at a heating rate of 2° C. / min for calcination to obtain a pale yellow solid powder material, which is ground evenly and used for later use.
[0059] b. Take 0.1 g of the light yellow solid powder material obtained in step a and place it in 30 mL of deionized water, and stir fully to obtain a uniformly dispersed g-C 3 N 4 / water mixed solution;
[0060] c. Add 0.40 mL of AgNO with a concentration of 1 mg / mL dropwise 3 solution, so that the Ag loading is controlled at 1.43% (mass fraction);
[0061] d, adding AgNO in step c 3 g-C 3 N 4 / Water mixed solution is ultrasonically treated, and a uniform pale yellow suspension is obtained after ultrasonication f...
PUM
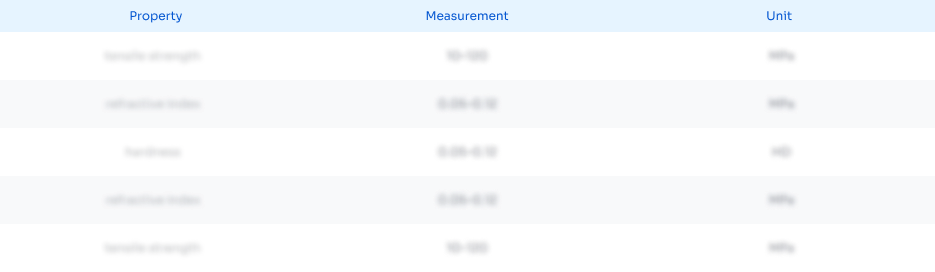
Abstract
Description
Claims
Application Information

- Generate Ideas
- Intellectual Property
- Life Sciences
- Materials
- Tech Scout
- Unparalleled Data Quality
- Higher Quality Content
- 60% Fewer Hallucinations
Browse by: Latest US Patents, China's latest patents, Technical Efficacy Thesaurus, Application Domain, Technology Topic, Popular Technical Reports.
© 2025 PatSnap. All rights reserved.Legal|Privacy policy|Modern Slavery Act Transparency Statement|Sitemap|About US| Contact US: help@patsnap.com