Method for preparing polyester polyol by recovering white mud and/or PET (Polyethylene Terephthalate)
A polyester polyol and white mud technology, applied in chemical instruments and methods, separation methods, plastic recycling, etc., can solve the problem of difficulty in obtaining satisfactory recycling efficiency and economic benefits, a large number of secondary three waste pollutants, and the quality of terephthalic acid. Low problems, to achieve the effect of reducing the probability of entering the filtrate, improving the hue and quality, and reducing the probability of agglomeration
- Summary
- Abstract
- Description
- Claims
- Application Information
AI Technical Summary
Problems solved by technology
Method used
Image
Examples
Embodiment 1
[0050] A method for recovering white mud and / or PET to prepare polyester polyol, the preparation steps comprising:
[0051] The PET recovered in S1 is subjected to crushing, alkali washing, water washing, filtration and drying; the recovered PET is mixed with diethylene glycol, an alcoholysis catalyst is added, and at the same time, in the presence of ultrasonic waves, the alcoholysis reaction is carried out with stirring, and the reaction temperature is 150~ 190℃, N 2 Pressurize and react under pressure of 5.0-8.0 MPa for 1-1.5 h to obtain an alcoholysis product; the molar ratio of PET to diol is 1:1.5;
[0052] The ultrasonic frequency used: 20KHZ, power: 2800W;
[0053] The alcoholysis catalyst is a mixture of zinc acetate and the ionic liquid [Bmim]Br catalyst in a molar ratio of 1:1, and the alcoholysis catalyst accounts for 0.5% of the recovered PET mass;
[0054] S2 maintains the alcoholysis product obtained in step S1 to filter under a high temperature state, and the...
Embodiment 2
[0079]A method for recovering white mud and / or PET to prepare polyester polyol, the preparation steps comprising:
[0080] The acid-treated alkali-reduced white mud and PTA pool material recovered by S1 were added with diethylene glycol in a mass ratio of 1:1, and in the presence of an esterification catalyst, a pre-esterification reaction was carried out, and the reaction temperature was 200-245 ° C to obtain a pre-esterification reaction. polymer; the molar ratio of terephthalic acid and dihydric alcohol in described alkali reduction white mud and PTA pool material is 1:1.5;
[0081] S2 maintains the alcoholysis product or prepolymer obtained in step S1 to filter under a high temperature state, and the filtration temperature is > 220 ° C;
[0082] In the filtration process, stainless steel wire mesh is used for filtration, and the mesh diameter is less than or equal to 20 μm;
[0083] S3 cools down the alcoholysis product and / or the prepolymer filtrate obtained in step S2 t...
Embodiment 3
[0098] A method for recovering white mud and / or PET to prepare polyester polyol, the preparation steps comprising:
[0099] The PET recovered from S1 is crushed, washed with alkali, washed with water, filtered and dried; the recovered PET is mixed with diethylene glycol, and an alcoholysis catalyst is added. 190℃, N 2 Pressurize, react 1~1.5h under pressure 5.0~8.0MPa, obtain alcoholysis product; The mol ratio of described PET and dihydric alcohol is 1: 2;
[0100] The ultrasonic frequency used: 20KHZ, power: 2800W;
[0101] The alcoholysis catalyst is a mixture of zinc acetate and the ionic liquid [Bmim]Br catalyst in a molar ratio of 1:1, and the alcoholysis catalyst accounts for 0.8% of the recovered PET mass;
[0102] The recovered acid-treated alkali-reduced white mud is added with diethylene glycol, and in the presence of an esterification catalyst, a pre-esterification reaction is carried out, and the reaction temperature is 200 to 245° C. to obtain a prepolymer; the ...
PUM
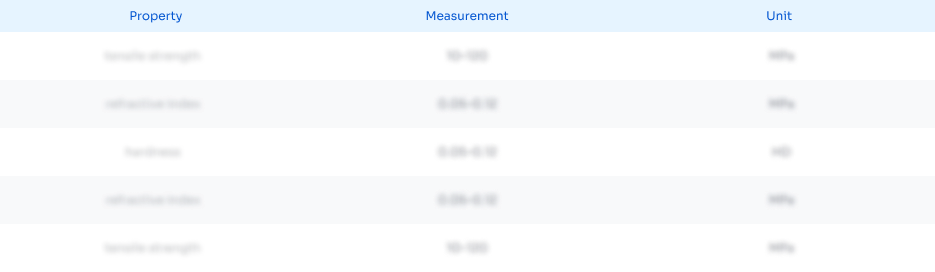
Abstract
Description
Claims
Application Information

- R&D Engineer
- R&D Manager
- IP Professional
- Industry Leading Data Capabilities
- Powerful AI technology
- Patent DNA Extraction
Browse by: Latest US Patents, China's latest patents, Technical Efficacy Thesaurus, Application Domain, Technology Topic, Popular Technical Reports.
© 2024 PatSnap. All rights reserved.Legal|Privacy policy|Modern Slavery Act Transparency Statement|Sitemap|About US| Contact US: help@patsnap.com