Smelting method for reducing nitrogen increase of molten steel in converter process
A smelting method and converter technology, applied in the field of iron and steel metallurgy, can solve the problems of steel toughness, plasticity, deep drawing, hot working and welding performance degradation, intergranular corrosion, slab cracking and other problems, and achieve novel methods and reduce molten steel. The effect of nitrogen absorption and reduction of contact frequency
- Summary
- Abstract
- Description
- Claims
- Application Information
AI Technical Summary
Problems solved by technology
Method used
Image
Examples
Embodiment 1
[0022] In this embodiment, the smelting of high-strength steel Q960D is taken as an example to explain the technical solution of the present invention in detail. In this embodiment, W[N] of molten steel is required to be less than or equal to 40×10 -4 %. The specific implementation process is as follows:
[0023] (1) Loading system: molten iron + scrap steel is used for smelting, of which the proportion of molten iron is 82% and the proportion of scrap steel is 18%; it is not allowed to use molten molten steel for smelting;
[0024] (2) Scrap quality: the source of scrap is not limited, and w[N] in scrap is 100×10 -4 %; the length × width × thickness of the scrap steel is 1.5m × 1.5m × 0.3m, and it is completely dissolved in the early stage of smelting;
[0025] (3) Requirements for argon blowing at the bottom of the converter: in the early stage of smelting, due to the violent reaction of C-O in the molten pool, the molten pool has good nitrogen removal capacity. Therefore...
Embodiment 2
[0032] In this embodiment, the smelting of high-strength steel Q960D is taken as an example to explain the technical solution of the present invention in detail. In this embodiment, W[N] of molten steel is required to be less than or equal to 40×10 -4 %. The specific implementation process is as follows:
[0033] (1) Loading system: molten iron + scrap steel is used for smelting, of which the proportion of molten iron is 83% and the proportion of scrap steel is 17%; it is not allowed to use molten molten steel for smelting;
[0034] (2) Scrap quality: select high-quality low-nitrogen scrap, and w[N] in the scrap is 90×10 -4 %; the length × width × thickness of the scrap steel is 1.4m × 1.4m × 0.28m, and it is completely dissolved in the early stage of smelting;
[0035] (3) Requirements for argon blowing at the bottom of the converter: in the early stage of smelting, due to the violent reaction of C-O in the molten pool, the molten pool has a good ability to remove nitrogen...
Embodiment 3
[0042] In this embodiment, the smelting of high-strength steel Q960D is taken as an example to explain the technical solution of the present invention in detail. In this embodiment, W[N] of molten steel is required to be less than or equal to 40×10 -4 %, the specific implementation process is as follows:
[0043] (1) Loading system: molten iron + scrap steel is used for smelting, of which the proportion of molten iron is 85% and the proportion of scrap steel is 15%; it is not allowed to use molten molten steel for smelting;
[0044] (2) Scrap quality: select high-quality low-nitrogen scrap, and w[N] in the scrap is 80×10 -4 %; the length × width × thickness of scrap steel is 1.3m × 1.3m × 0.25m, and it is completely dissolved in the early stage of smelting;
[0045] (3) Requirements for argon blowing at the bottom of the converter: in the early stage of smelting, due to the violent reaction of C-O in the molten pool, the molten pool has a good ability to remove nitrogen, so ...
PUM
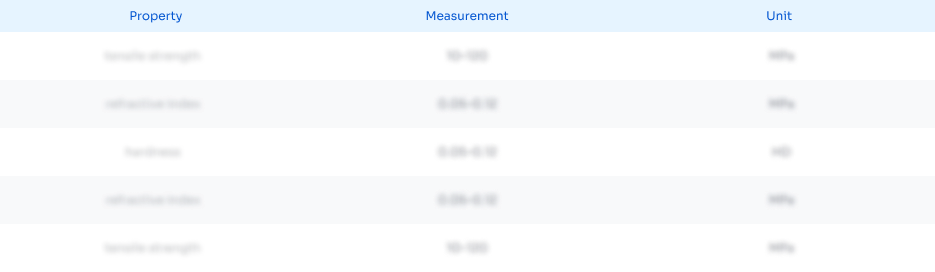
Abstract
Description
Claims
Application Information

- R&D
- Intellectual Property
- Life Sciences
- Materials
- Tech Scout
- Unparalleled Data Quality
- Higher Quality Content
- 60% Fewer Hallucinations
Browse by: Latest US Patents, China's latest patents, Technical Efficacy Thesaurus, Application Domain, Technology Topic, Popular Technical Reports.
© 2025 PatSnap. All rights reserved.Legal|Privacy policy|Modern Slavery Act Transparency Statement|Sitemap|About US| Contact US: help@patsnap.com