Preparation method of A-grade modified polystyrene board
A polystyrene board, modified technology, applied in the field of construction, can solve the problems of high thermal conductivity, high apparent density, poor thermal insulation effect, etc., to achieve the effect of reducing thermal conductivity, reducing apparent density, and reducing cement consumption
- Summary
- Abstract
- Description
- Claims
- Application Information
AI Technical Summary
Problems solved by technology
Method used
Image
Examples
Embodiment 1
[0017] Please refer to figure 1 , a preparation method of A-level modified polystyrene board, comprising the steps:
[0018] S1, pre-expanding to obtain pre-expanded polystyrene particles with a preset bulk density;
[0019] The step S1 is specifically:
[0020] The expandable polystyrene beads are pre-expanded to obtain pre-expanded polystyrene particles with a preset bulk density, where the preset bulk density is 4-15 kg / cubic.
[0021] Preferably, when the preset bulk density is 5-10 kg / m3, the obtained A-grade modified polystyrene board has significantly improved thermal insulation performance, and the pre-foaming process is a primary foaming process or a secondary foaming process.
[0022] S2, coating the pre-expanded polystyrene particles once with inorganic silicate composite raw materials, and drying and dispersing to obtain a coating mixture;
[0023] The inorganic silicate composite raw materials are recorded in parts by weight as 50-70 parts of silicate, 5-10 par...
Embodiment 2
[0034] 1) Screening pre-expanded polystyrene particles with a bulk density of 5 kg / cubic;
[0035] 2) Weigh 60 parts of potassium silicate solution, 10 parts of emulsion, 4 parts of redispersible rubber powder, 1 part of silane coupling agent, and 15 parts of water, after mixing evenly, add the pre-foamed polyphenylene in step 1). vinyl pellets, one coat;
[0036] 3) The polystyrene particles after the primary coating are transferred to an oven at 65° C. for drying for 8 hours, during which stirring and dispersing is performed, and the primary coating polystyrene particles in a dry and dispersed state are finally obtained;
[0037] 4) Weigh 600 parts of Portland cement, 50 parts of vitrified microbeads, 20 parts of hollow glass microbeads, 6 parts of calcium formate, 2 parts of glass fiber, 2 parts of cellulose, 4 parts of redispersible rubber powder, organic 1 part of silicon, after fully mixing, add 315 parts of water to prepare a secondary coating material;
[0038] 5) fu...
Embodiment 3
[0041] 1) Screening pre-expanded polystyrene particles with a bulk density of 6 kg / cubic;
[0042] 2) Weigh 50 parts of potassium silicate, 10 parts of lithium silicate, 10 parts of emulsion, 4 parts of redispersible rubber powder, 1 part of silane coupling agent, and 15 parts of water. Pre-expanded polystyrene particles, one coating;
[0043] 3) The polystyrene particles after the primary coating are transferred to an oven at 65° C. for drying for 8 hours, during which stirring and dispersing is performed, and the primary coating polystyrene particles in a dry and dispersed state are finally obtained;
[0044] 4) Weigh 600 parts of Portland cement, 20 parts of vitrified microbeads, 50 parts of hollow glass microbeads, 6 parts of calcium formate, 2 parts of glass fiber, 2 parts of cellulose, 4 parts of redispersible rubber powder, organic 1 part of silicon, after fully mixing, add 315 parts of water to prepare a secondary coating material;
[0045] 5) fully mix the material ...
PUM
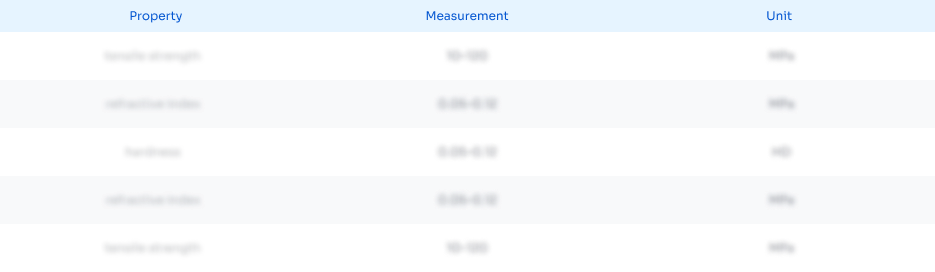
Abstract
Description
Claims
Application Information

- R&D Engineer
- R&D Manager
- IP Professional
- Industry Leading Data Capabilities
- Powerful AI technology
- Patent DNA Extraction
Browse by: Latest US Patents, China's latest patents, Technical Efficacy Thesaurus, Application Domain, Technology Topic, Popular Technical Reports.
© 2024 PatSnap. All rights reserved.Legal|Privacy policy|Modern Slavery Act Transparency Statement|Sitemap|About US| Contact US: help@patsnap.com