Anticorrosive waterborne epoxy coating based on divalent zinc ions and phytic acid modified graphene oxide and preparation method of anticorrosive waterborne epoxy coating
A technology of water-based epoxy and water-based epoxy resin, which is applied in the direction of anti-corrosion coatings, epoxy resin coatings, coatings, etc., can solve the problems of blocking the corrosion process, poor compactness of water-based epoxy coatings and cannot effectively block, and achieve improved Dispersion, enhance the ability to resist chloride ion corrosion, improve the effect of anti-corrosion performance
- Summary
- Abstract
- Description
- Claims
- Application Information
AI Technical Summary
Problems solved by technology
Method used
Image
Examples
preparation example Construction
[0027] The invention provides an anti-corrosion coating based on modified graphene of phytic acid and hexahydrate zinc nitrate and a preparation method thereof. The process of the method is as follows: adding phytic acid, hexahydrate zinc nitrate and graphene oxide into water, and dispersing evenly Then react at room temperature to obtain modified graphene; after dispersing the modified graphene in deionized water, add it to the mixed solution of resin and curing agent and disperse evenly to obtain the modified graphene based on phytic acid and divalent zinc ions. Graphene coating mixture. The coating mixture is coated on the surface of the metal substrate, and cured at room temperature to form a film to obtain a metal anti-corrosion coating.
[0028] Preferably, the amount of modified graphene oxide added in the coating is 0.05wt% to 0.10wt%.
[0029] Preferably, the divalent zinc ion precursor in the preparation process of the modified graphene oxide is zinc nitrate hexahyd...
Embodiment 1
[0040] This embodiment is the preparation of GO@(Zn(II)-PA) / WEC coating, as follows:
[0041] 1. Filler preparation: Take 20ml of GO solution with a concentration of 2mg / ml and add it to 140ml of deionized water for ultrasonic dispersion for 15min, and adjust the pH of the above GO solution to 8.0 by adding 0.1mol / L NaOH solution dropwise. Add 300mg Zn(NO 3 ) 2 ·6H 2 O, after magnetic stirring at room temperature at 560 rpm for 1 hour; then add 2.856 g of PA solution with a concentration of 70 wt.%, and also at room temperature at 560 rpm with magnetic stirring for 1 hour. After the reaction, ultrasonically cleaned with deionized water for 10 minutes, centrifuged at 10,000 r / min for 3 minutes, and repeatedly cleaned for 3 times to obtain GO@(Zn(II)-PA) filler.
[0042] 2. Coating preparation: Take 2.5mg of the above-obtained GO@(Zn(II)-PA) filler and put it in 1ml of deionized water, after ultrasonic dispersion for 15min, mix with 2.13g of water-based epoxy The ratio is 5:...
Embodiment 2
[0044] This embodiment is the preparation of GO@(Zn(II)-PA) / WEC coating, as follows:
[0045] 1. Filler preparation: 15ml of GO solution with a concentration of 2mg / ml was added to 100ml of deionized water for ultrasonic dispersion for 15min, and the pH of the above GO solution was adjusted to 8.0 by dropwise addition of 0.1mol / L NaOH solution. Add 200mg Zn(NO 3 ) 2 ·6H 2 O, after stirring at room temperature at 600 rpm for 1 hour; then add 2.0 g of PA solution with a concentration of 70 wt.%, and also stir at room temperature at 560 rpm for 1 hour. After the reaction, ultrasonically cleaned with deionized water for 10 minutes, centrifuged at 10,000 r / min for 3 minutes, and repeatedly cleaned for 3 times to obtain GO@(Zn(II)-PA) filler.
[0046] 2. Coating preparation: Take 2.5mg of the above-obtained GO@(Zn(II)-PA) filler and put it in 1ml of deionized water, after ultrasonic dispersion for 15min, mix with 2.13g of water-based epoxy The ratio is 5:9) stir well and let sta...
PUM
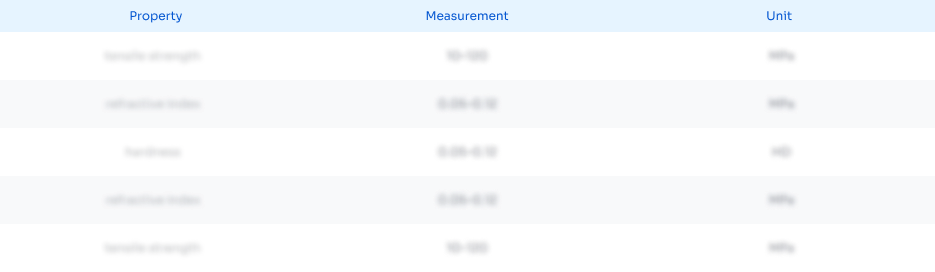
Abstract
Description
Claims
Application Information

- Generate Ideas
- Intellectual Property
- Life Sciences
- Materials
- Tech Scout
- Unparalleled Data Quality
- Higher Quality Content
- 60% Fewer Hallucinations
Browse by: Latest US Patents, China's latest patents, Technical Efficacy Thesaurus, Application Domain, Technology Topic, Popular Technical Reports.
© 2025 PatSnap. All rights reserved.Legal|Privacy policy|Modern Slavery Act Transparency Statement|Sitemap|About US| Contact US: help@patsnap.com