Preparation method of high-dispersion white carbon black
A high-dispersion white carbon black, a certain amount of technology, applied in the field of rubber additives, can solve the problems such as the inability to meet the development needs of high-performance green tires, the comprehensive performance of easy-to-agglomerate rubber composite materials, and the poor dispersibility. Rubber properties, the effect of reducing agglomeration and increasing crosslinking density
- Summary
- Abstract
- Description
- Claims
- Application Information
AI Technical Summary
Problems solved by technology
Method used
Image
Examples
Embodiment 1
[0021] A preparation method of high-dispersion white carbon black for rubber reinforcement, the specific steps are as follows:
[0022] S1: The nano-SiO 2 and D-sodium gluconate (0.05%) were dispersed in deionized water, after ultrasonic dispersion for 0.5-1.5h, anhydrous Na was added to the suspension 2 CO 3 And stir and dissolve completely to obtain solution A;
[0023] S2: Weigh a certain amount of Mg(NO 3 ) 2 ·6H 2 O, Ca(NO 3 ) 2 ·6H 2 O, Al (NO 3 ) 3 ·9H 2 O was dissolved in deionized water to form solution B, in which SiO 2 and Mg x-nCanAl - The mass ratio of LDH is 5:1, the value of x is 3, and the value of n is 0.2, indicating that n (Mg 2+ +Ca 2+ ): n (Al 3+ ) is 3:1, n(Ca 2+ ): n(Al 3+ ) is 0.2:1;
[0024] S3: Slowly add solution B to solution A at room temperature, stir slowly, and add 1 mol / L NaOH solution to control the pH value of the solution to 11. After aging for 18 hours, wash, centrifugal spray and dry to obtain nano-SiO 2 -Mg 2.8 Ca 0.2...
Embodiment 2
[0027] A preparation method of high-dispersion white carbon black for rubber reinforcement, the specific steps are as follows:
[0028] S1: The nano-SiO 2 and D-sodium gluconate (0.8%) were dispersed in deionized water, after ultrasonic dispersion for 1 h, anhydrous Na was added to the suspension 2 CO 3 And stir and dissolve completely to obtain solution A;
[0029] S2: Weigh a certain amount of Mg(NO 3 ) 2 ·6H 2 O, Ca(NO 3 ) 2 ·6H 2 O, Al (NO 3 ) 3 ·9H 2 O was dissolved in deionized water to form solution B, in which SiO 2 and Mg x-nCanAl - The mass ratio of LDH is 5:3, the value of x is 3, and the value of n is 0.4, indicating that n (Mg 2+ +Ca 2+ ): n (Al 3+ ) is 3:1, n(Ca 2+ ): n(Al 3+ ) is 0.4:1;
[0030] S3: slowly add solution B to solution A at room temperature, stir slowly, and add 1 mol / L NaOH solution to control the pH value of the solution to be 11, after aging for 18h, wash, centrifugal spray and dry to obtain nano-SiO 2 -Mg 2.6 Ca 0.4 Al-LDH...
Embodiment 3
[0033] A preparation method of high-dispersion white carbon black for rubber reinforcement, the specific steps are as follows:
[0034]S1: The nano-SiO 2 and sodium D-gluconate (1%) were dispersed in deionized water, after ultrasonic dispersion for 1 h, anhydrous Na was added to the suspension 2 CO 3 And stir and dissolve completely to obtain solution A;
[0035] S2: Weigh a certain amount of Mg(NO 3 ) 2 ·6H 2 O, Ca(NO 3 ) 2 ·6H 2 O, Al (NO 3 ) 3 ·9H 2 O was dissolved in deionized water to form solution B, in which SiO 2 and Mg x-nCanAl - The mass ratio of LDH is 1:1, the value of x is 3, and the value of n is 0.8, indicating that n (Mg 2+ +Ca 2+ ): n (Al 3+ ) is 3:1, n(Ca 2+ ): n(Al 3+ ) is 0.8:1;
[0036] S3: slowly add solution B to solution A at room temperature, stir slowly, and add 1 mol / L NaOH solution to control the pH value of the solution to be 11, after aging for 18h, wash, centrifugal spray and dry to obtain nano-SiO 2 -Mg 2.2 Ca 0.8 Al-LDH co...
PUM
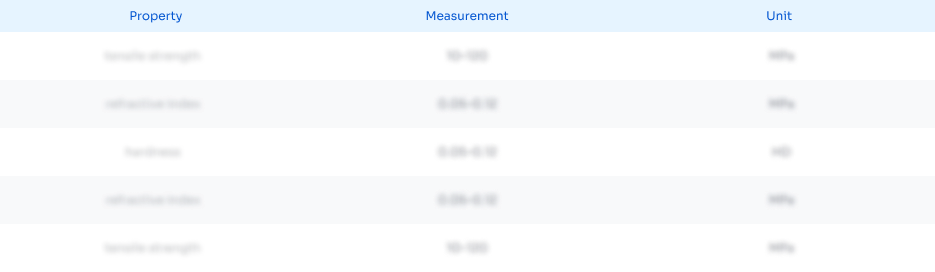
Abstract
Description
Claims
Application Information

- R&D Engineer
- R&D Manager
- IP Professional
- Industry Leading Data Capabilities
- Powerful AI technology
- Patent DNA Extraction
Browse by: Latest US Patents, China's latest patents, Technical Efficacy Thesaurus, Application Domain, Technology Topic, Popular Technical Reports.
© 2024 PatSnap. All rights reserved.Legal|Privacy policy|Modern Slavery Act Transparency Statement|Sitemap|About US| Contact US: help@patsnap.com