Nanometer silicon dioxide reinforcing and toughening master batch and preparation method thereof
A nano-silica, reinforcement and toughening technology, applied in the field of plastic modification, can solve the problems of lower polyethylene performance, high surface energy, and easy aggregation of nanoparticles, so as to increase compatibility and improve modification effect Effect
- Summary
- Abstract
- Description
- Claims
- Application Information
AI Technical Summary
Problems solved by technology
Method used
Image
Examples
Embodiment 1
[0013] 1. Turn on the co-rotating parallel twin-screw extruder for heating. The heating temperature of each temperature zone is as follows:
[0014]
[0015] 2. Clean up the high-speed mixer, and weigh 0.7 parts of zinc stearate, 0.5 parts of coupling agent, 20 parts of nano-silicon dioxide, 74 parts of polyethylene, and 5 parts of magnesium hydroxystearate according to the formula. , first add the coupling agent and nano-silica into the high-speed mixer, first stir at low speed for 6 to 8 minutes, and then use high-speed stirring to 70℃-80℃, so that the coupling agent evenly coats the nano-silica, and then Add the remaining materials to the high-speed mixer and mix at high speed for 15 minutes to fully mix the materials evenly.
[0016] 3. When the temperature rises to the temperature in the above table, add the stirred raw materials into the feeding hopper of the co-rotating parallel twin-screw extruder, turn on the oil pump, water pump, vacuum pump, blow dryer, and pelle...
Embodiment 2
[0018] 1. Turn on the twin-screw extruder for heating. The heating temperature of each temperature zone is as follows:
[0019]
[0020] 2. Clean up the high-speed mixer, and weigh 1 part of zinc stearate, 0.8 part of coupling agent, 25 parts of nano-silicon dioxide, 67.2 parts of polyethylene, and 6 parts of magnesium hydroxystearate according to the formula. , First add the coupling agent and nano-silica into the high-speed mixer, first stir at low speed for 6 to 8 minutes, and then use high-speed stirring to 70-80 ℃, so that the coupling agent evenly coats the nano-silica. Then add the remaining materials together into the high-speed mixer and stir at a high speed for 15 minutes to fully mix the materials evenly.
[0021] 3. When the temperature rises to the temperature in the above table, add the stirred raw materials into the feeding hopper of the co-rotating parallel twin-screw extruder, turn on the oil pump, water pump, vacuum pump, blow dryer, and pelletizer in turn...
Embodiment 3
[0023] 1. Turn on the twin-screw extruder for heating. The heating temperature of each temperature zone is as follows:
[0024]
[0025] 2. Clean up the high-speed mixer, and weigh 1 part of zinc stearate, 0.9 part of coupling agent, 30 parts of nano-silicon dioxide, 62.1 parts of polyethylene, and 6 parts of magnesium hydroxystearate according to the formula. , First add the coupling agent and nano-silica into the high-speed mixer, first stir at low speed for 6 to 8 minutes, and then use high-speed stirring to 70-80 ℃, so that the coupling agent evenly coats the nano-silica. Then add the remaining materials together into the high-speed mixer and stir at a high speed for 17 minutes to fully mix the materials evenly.
[0026] 3. When the temperature rises to the temperature in the above table, add the stirred raw materials into the feeding hopper of the co-rotating parallel twin-screw extruder, turn on the oil pump, water pump, vacuum pump, blow dryer, and pelletizer in turn...
PUM
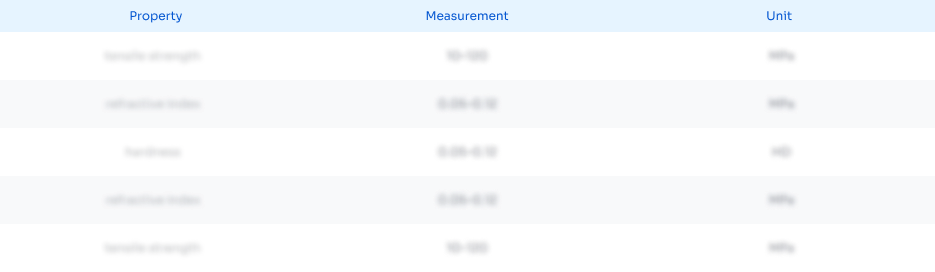
Abstract
Description
Claims
Application Information

- Generate Ideas
- Intellectual Property
- Life Sciences
- Materials
- Tech Scout
- Unparalleled Data Quality
- Higher Quality Content
- 60% Fewer Hallucinations
Browse by: Latest US Patents, China's latest patents, Technical Efficacy Thesaurus, Application Domain, Technology Topic, Popular Technical Reports.
© 2025 PatSnap. All rights reserved.Legal|Privacy policy|Modern Slavery Act Transparency Statement|Sitemap|About US| Contact US: help@patsnap.com