Variable-stiffness variable-damping magnetorheological fluid vibration reduction boring bar
A technology of magnetorheological fluid and variable damping, applied to boring bars and other directions, can solve the problems of boring bar machining accuracy and machining efficiency, and achieve the effects of reducing boring bar vibration, changing damping, and improving machining efficiency.
- Summary
- Abstract
- Description
- Claims
- Application Information
AI Technical Summary
Problems solved by technology
Method used
Image
Examples
specific Embodiment approach 1
[0023] Embodiment 1: Combining Figure 1 to Figure 5 Illustrating this embodiment, a variable stiffness variable damping magnetorheological fluid vibration damping boring bar described in this embodiment includes a cutter head connecting block 2, a coil 6, a cylinder block 7, a rod body 8, a cylinder head 9, a cantilever beam 12, Iron core 13, telescopic rod 15, slider 16, lead screw 17, stepper motor 18 and control system 19, the middle of the front end face of the rod body 8 is provided with a boring bar cavity 8-1, and the rear side of the cutter head connecting block 2 The end is inserted into the cavity mouth of the boring bar cavity 8-1, the front end of the cantilever beam 12 is vertically fixed to the middle of the rear end face of the cutter head connecting block 2, and the cylinder body 7 is inserted into the boring bar cavity 8-1. The front end of the cylinder block 7 is fixed with the cylinder head 9 , the rear end of the cantilever beam 12 passes through the cylin...
specific Embodiment approach 2
[0029] Specific implementation mode 2: Combining Figure 1 to Figure 5 Illustrating this embodiment, the outer side of the iron core 13 described in this embodiment is sheathed with a rubber sleeve 1 14 . Other compositions and connection methods are the same as those in the first embodiment.
[0030] The rubber sleeve 14 is inserted into the outer side of the iron core 13 to protect the coil 6 from being affected by the magnetorheological fluid 4 .
specific Embodiment approach 3
[0031] Specific implementation three: combination Figure 1 to Figure 5 Describing the present embodiment, the outer side of the cylinder block 7 described in the present embodiment is sheathed with a rubber sleeve 2 5 . Other compositions and connection methods are the same as those in the first embodiment.
[0032] In this embodiment, the second rubber sleeve 5 is fixedly connected to the outer side of the cylinder block 7 to ensure that the entire cylinder block 7 can slide in the boring bar cavity 8-1.
PUM
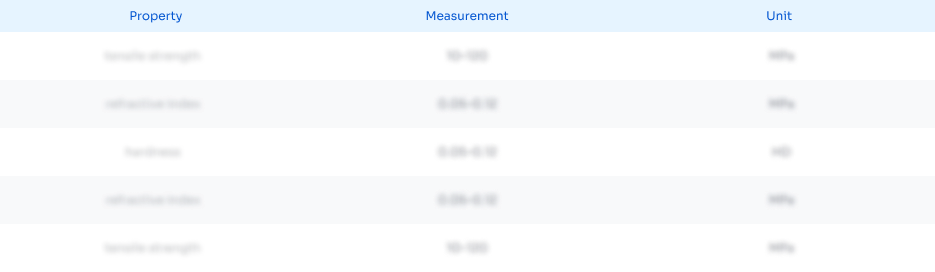
Abstract
Description
Claims
Application Information

- R&D
- Intellectual Property
- Life Sciences
- Materials
- Tech Scout
- Unparalleled Data Quality
- Higher Quality Content
- 60% Fewer Hallucinations
Browse by: Latest US Patents, China's latest patents, Technical Efficacy Thesaurus, Application Domain, Technology Topic, Popular Technical Reports.
© 2025 PatSnap. All rights reserved.Legal|Privacy policy|Modern Slavery Act Transparency Statement|Sitemap|About US| Contact US: help@patsnap.com