Formula of high-hardness easy-to-produce nitrile rubber
A nitrile rubber and formulation technology, which is applied in the field of high-hardness and easy-to-produce nitrile-butadiene rubber formulations, can solve the problems of poor rubber fluidity and high NBR hardness drop rate, and achieves easy processing of rubber materials, reduced hardness drop rate, and qualified product appearance. high rate effect
- Summary
- Abstract
- Description
- Claims
- Application Information
AI Technical Summary
Problems solved by technology
Method used
Image
Examples
Embodiment 1
[0020] The invention is a high-hardness and easy-to-produce nitrile-butadiene rubber formula, and the NBR formula is composed of the following raw materials: 33.0 parts of NBR+PVC rubber-plastic alloy; 36.0 parts of carbon black; 1.7 parts of softener; 3.0 parts of active agent; 2.9 parts of anti-aging agent; 1.2 parts of accelerator; 3.0 parts of phenolic resin; 0.6 part of modified hexamethylenetetramine.
[0021] Further, carbon black is used as a reinforcing agent as a filler to improve the strength of rubber products. The consumption of carbon black generally accounts for 40% to 50% of the consumption of rubber. Usually, 2 parts of rubber are used together with 1 part. carbon black; NBR+PVC rubber-plastic alloy refers to the mixture of nitrile rubber and polyvinyl chloride, and the weight of polyvinyl chloride is 20% to 30% of the weight of butadiene rubber.
[0022] Further, softener is a foam additive with softening effect under higher chemical foaming agent water consu...
Embodiment 2
[0029] When using this high-hardness and easy-to-produce NBR formula for rubber production, appropriately reduce the amount of carbon black added, reasonably adjust the fluidity requirements of the rubber compound, add phenolic resin and modified hexamethylenetetramine, and the material and rubber during high temperature vulcanization. The polymer undergoes chemical cross-linking, the cross-density increases, and the hardness reaches more than 90 degrees. After the product is heated, the hardness decrease rate is greatly reduced. The phenolic resin is generally added at 8-15%, and the modified hexamethylenetetramine is generally added at 0.6 -1.2% is added. After the two are properly matched, the rubber material is easy to process, the film is smooth and flat, the rubber material has good fluidity, the product has a thin burr, and the product appearance qualification rate is over 99%.
Embodiment 3
[0031] According to whether phenolic resin and modified hexamethylenetetramine are added to the NBR formula, the hardness of the rubber produced is compared, and the rubber without phenolic resin and modified hexamethylenetetramine is selected as the control group, and the rubber with phenolic resin is selected as the control group. As group A, the modified hexamethylenetetramine was selected as the B group, and the phenolic resin and modified hexamethylenetetramine were selected as the C group. The configured rubber hardness is shown in the table below:
[0032] Table 1: Rubber hardness prepared with different additives
[0033]
[0034]
[0035] It can be seen from the above table that the rubber hardness produced by the formula with the addition of phenolic resin and modified hexamethylenetetramine is the highest.
PUM
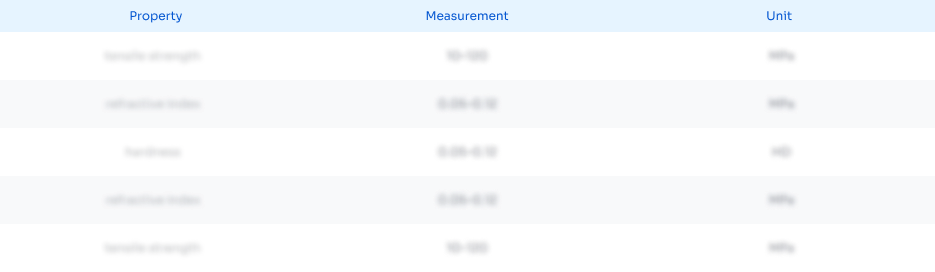
Abstract
Description
Claims
Application Information

- R&D
- Intellectual Property
- Life Sciences
- Materials
- Tech Scout
- Unparalleled Data Quality
- Higher Quality Content
- 60% Fewer Hallucinations
Browse by: Latest US Patents, China's latest patents, Technical Efficacy Thesaurus, Application Domain, Technology Topic, Popular Technical Reports.
© 2025 PatSnap. All rights reserved.Legal|Privacy policy|Modern Slavery Act Transparency Statement|Sitemap|About US| Contact US: help@patsnap.com