Good-appearance low-carbon environment-friendly fiber-reinforced PC/PLA composite material and preparation method thereof
A low-carbon, environmentally friendly, composite material technology, applied in the field of good appearance, low-carbon and environmentally friendly glass fiber reinforced PC/PLA composite materials and its preparation, can solve the problem of affecting people's living environment and ecological environment, the difficulty of recycling glass fiber reinforced PC, and the recycling of recycled materials. Problems such as large performance attenuation, to achieve the effect of maintaining long-term stability, promoting development and application, and improving processing plasticity
- Summary
- Abstract
- Description
- Claims
- Application Information
AI Technical Summary
Problems solved by technology
Method used
Image
Examples
Embodiment 1
[0043]Dry PC and PC recycled materials in a dehumidification dryer at 100°C for 4-6 hours, and dry PLA raw materials in a dehumidification dryer at 70°C for 4-6 hours to ensure that the moisture content is within 0.08%.
[0044] After drying, 30 parts of PC, 20 parts of PLA, 20 parts of recycled PC, 5 parts of EM500, 4 parts of PBAT-MAH, 10 parts of PMMA, 0.3 parts of antioxidant, 0.5 parts of lubricant, and 0.2 parts of transesterification inhibitor , 1 part of anti-hydrolysis agent, 3 parts of plasticizer, and 0.3 part of chain extender were mixed in a high-speed mixer at 80°C for 10 minutes, and then added to a twin-screw extruder with a length-to-diameter ratio of 40:1 from the main feeding port. At the same time, 10 parts of chopped glass fibers are added from the side feed port, and then granulated after being melted and extruded by a twin-screw extruder to obtain a degradable biocomposite material, wherein the processing temperature of the twin-screw extruder is 160°C ℃...
Embodiment 2
[0046] Place PC and PC recycled materials in a dehumidification dryer at 100°C for drying, and place PLA raw materials in a dehumidification dryer for drying at 70°C to ensure that their moisture content is within 0.08%.
[0047] 15 parts of dried PC, 40 parts of PLA, 8 parts of recycled PC and 10 parts of EM500 agent, 8 parts of PBAT-MAH, 12 parts of PMMA, 0.3 parts of antioxidant, 0.5 parts of lubricant, 0.5 parts of transesterification inhibitor , 2 parts of anti-hydrolysis agent, 5 parts of plasticizer, and 0.5 part of chain extender are mixed in a high-speed mixer at 80°C for 10 minutes, and then added to a twin-screw extruder with a length-to-diameter ratio of 40:1 from the main feeding port. At the same time, 10 parts of chopped glass fibers are added from the side feed port, and then granulated after being melted and extruded by a twin-screw extruder to obtain a degradable biocomposite material, wherein the processing temperature of the twin-screw extruder is 160°C ℃, ...
Embodiment 3
[0049] Place PC and PC recycled materials in a dehumidification dryer at 100°C for drying, and place PLA raw materials in a dehumidification dryer for drying at 70°C to ensure that their moisture content is within 0.08%.
[0050] 26 parts of dried PC, 30 parts of PLA, 5 parts of recycled PC and 8 parts of EM500, 5 parts of PBAT-MAH, 10 parts of PMMA, 0.3 parts of antioxidant, 0.4 parts of lubricant, 0.4 parts of transesterification inhibitor , 1.5 parts of anti-hydrolysis agent, 4 parts of plasticizer, and 0.4 parts of chain extender were mixed in a high-speed mixer at 80°C for 10 minutes, and then added into a twin-screw extruder with a length-to-diameter ratio of 40:1 from the main feeding port. At the same time, 10 parts of chopped glass fibers are added from the side feed port, and then granulated after being melted and extruded by a twin-screw extruder to obtain a degradable biocomposite material, wherein the processing temperature of the twin-screw extruder is 160°C ℃, Z...
PUM
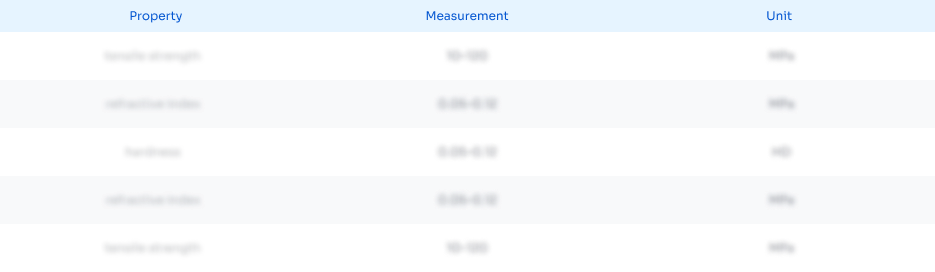
Abstract
Description
Claims
Application Information

- R&D
- Intellectual Property
- Life Sciences
- Materials
- Tech Scout
- Unparalleled Data Quality
- Higher Quality Content
- 60% Fewer Hallucinations
Browse by: Latest US Patents, China's latest patents, Technical Efficacy Thesaurus, Application Domain, Technology Topic, Popular Technical Reports.
© 2025 PatSnap. All rights reserved.Legal|Privacy policy|Modern Slavery Act Transparency Statement|Sitemap|About US| Contact US: help@patsnap.com