Methyl acrylate synthesis method, catalyst and application
A technology of methyl acrylate and catalyst, which is applied in the direction of catalyst carrier, catalyst activation/preparation, physical/chemical process catalyst, etc., can solve the problems of short catalytic activity retention time, poor methyl acrylate yield and selectivity, etc. Improve product selectivity, good economic and social benefits, and improve selectivity
- Summary
- Abstract
- Description
- Claims
- Application Information
AI Technical Summary
Problems solved by technology
Method used
Image
Examples
preparation example Construction
[0068] The preparation method of solid catalyst
[0069] The preparation method of solid base catalyst of the present invention comprises:
[0070] (i) providing a precursor salt solution containing a catalytic amount of an alkali metal element and 50 to 80 parts of a carrier;
[0071] (ii) the solution of the step (i) is mixed with a carrier to obtain a mixture;
[0072] (iii) calcining the mixture in step (ii), preferably at a calcining temperature of 400-600° C., to obtain the solid catalyst.
[0073] The precursor salt is preferably at least one of nitrate, carbonate and acetate.
[0074] Preferably, the alkali metal includes at least one selected from the group consisting of K, Rb and Cs.
[0075] In order to obtain a catalyst with better strength, the catalyst preparation preferably has a drying step after step (ii) and before step (iii). The specific drying process conditions can be reasonably determined by those skilled in the art without having to pay creative e...
Embodiment 1
[0085] 1. Catalyst preparation
[0086] Get 100 grams of cesium carbonate aqueous solution (containing cesium carbonate with Cs 2 O is 12 grams); mix with 60 grams of silica microspheres (microsphere diameter 2.5mm, BET method average pore diameter 22nm, BET method pore volume 1.1ml / g), leave standstill for 24 hours, then vacuum at 50°C Dry for 24 hours, and bake at 500° C. in an air atmosphere for 5 hours to obtain a finished catalyst.
[0087] 2. On-line reduction activation of catalyst and synthesis of methyl acrylate
[0088] Get each 6 grams of three parts of catalyzers, pack respectively in the fixed-bed reactor (inner diameter 16mm long 1500mm) of 3 serial connections, use N 2 After three replacements, the temperature of the three reactors was raised to 400 °C, and N 2 , the flow rate is 1000mL / min, the pressure is 0.08MPa, keep for 12 hours, and the activation is completed.
[0089] The temperature of the three reactors was lowered to 300°C, the pressure was adjust...
Embodiment 2
[0091] 1. Catalyst preparation
[0092] Get 100 grams of cesium carbonate aqueous solution (containing cesium carbonate with Cs 2 O is 12 grams); mix with 60 grams of silica microspheres (microsphere diameter 2.5mm, BET method average pore diameter 22nm, BET method pore volume 1.1ml / g), leave standstill for 24 hours, then vacuum at 50°C Dry for 24 hours, and bake at 500° C. in an air atmosphere for 5 hours to obtain a finished catalyst.
[0093] 2. On-line reduction activation of catalyst and synthesis of methyl acrylate
[0094] Get each 3 grams of six parts of catalyzers, pack respectively in 6 fixed-bed reactors (inside diameter 16mm long 1500mm) of packing into, use N 2 After three replacements, the temperature of the six reactors was raised to 400°C, and N 2 , the flow rate is 1000mL / min, the pressure is 0.08MPa, keep for 12 hours, and the activation is completed.
[0095] The temperature of the 6 reactors was lowered to 300°C, the pressure was adjusted to 0.5MPa, and...
PUM
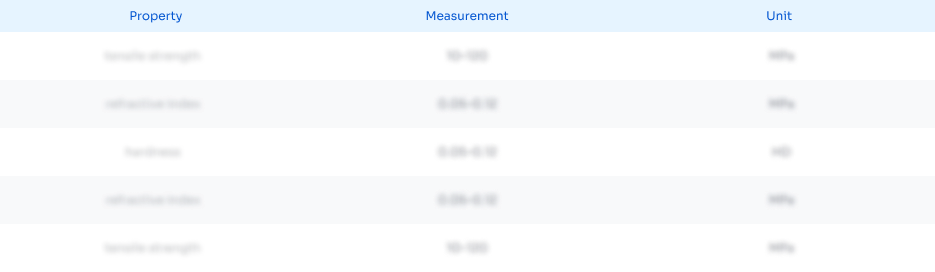
Abstract
Description
Claims
Application Information

- R&D
- Intellectual Property
- Life Sciences
- Materials
- Tech Scout
- Unparalleled Data Quality
- Higher Quality Content
- 60% Fewer Hallucinations
Browse by: Latest US Patents, China's latest patents, Technical Efficacy Thesaurus, Application Domain, Technology Topic, Popular Technical Reports.
© 2025 PatSnap. All rights reserved.Legal|Privacy policy|Modern Slavery Act Transparency Statement|Sitemap|About US| Contact US: help@patsnap.com