Catalytic cracking catalyst and preparation method thereof
A catalytic cracking and catalyst technology, applied in catalyst activation/preparation, catalytic cracking, physical/chemical process catalysts, etc., can solve the problems of high energy consumption, high loss, and complex catalytic cracking catalyst preparation
- Summary
- Abstract
- Description
- Claims
- Application Information
AI Technical Summary
Problems solved by technology
Method used
Image
Examples
preparation example Construction
[0044] In order to achieve the above object, a first aspect of the present invention provides a method for preparing a catalyst cracking catalyst, the method comprising:
[0045] 1) making the sodium-type molecular sieve and the solution containing the ammonium root ion carry out the first ion exchange reaction, and obtain the molecular sieve after the ammonium root ion exchange;
[0046] 2) Under microwave conditions, the ammonium ion-exchanged molecular sieve and the solution containing rare earth element ions are subjected to a second ion exchange reaction to obtain a molecular sieve containing rare earth elements;
[0047] 3) After beating the rare earth element-containing molecular sieve obtained in step 2) with clay, binder, water and inorganic acid to form a colloid, the obtained colloid is dried and calcined.
[0048] The inventors of the present invention have found that, firstly, the ammonium ion is used to exchange the sodium ions in the sodium-type molecular sieve,...
Embodiment 1
[0106] 1) NaY molecular sieve is mixed with ammonium ion concentration in ammonium chloride aqueous solution of 2mol / L, with respect to 1L ammonium chloride aqueous solution, the addition amount of NaY molecular sieve is 200g, adjusts pH with dilute hydrochloric acid solution (concentration is 5% by weight) After reaching 5.5, heat the above mixed solution to 70°C, and stir at this temperature for 30 minutes, then filter, wash the product with 5 times the volume of deionized water after filtration, and then dry it at 150°C for 6 hours to obtain ammonium ion-exchanged Molecular sieve;
[0107] 2) the molecular sieve after the ammonium ion exchange that step 1) obtains and total concentration are lanthanum chloride and cerium chloride aqueous solution (wherein, lanthanum chloride concentration is 0.2mol / L, and cerium chloride concentration is 0.3mol / L) mixing and beating, relative to 1L lanthanum chloride aqueous solution, the amount of molecular sieve after ammonium ion exchang...
Embodiment 2
[0115] 1) NaY molecular sieve is mixed with ammonium ion concentration in ammonium chloride aqueous solution of 2mol / L, with respect to 1L ammonium chloride aqueous solution, the addition amount of NaY molecular sieve is 200g, adjusts pH with dilute hydrochloric acid solution (concentration is 5% by weight) After reaching 6, heat the above mixed solution to 60°C, and stir at this temperature for 20 minutes, then filter, wash the obtained product with 5 times the volume of deionized water after filtration, and then dry at 150°C for 6 hours to obtain ammonium ion exchanged Molecular sieve;
[0116] 2) the molecular sieve after the ammonium ion exchange that step 1) obtains and total concentration are lanthanum chloride and cerium chloride aqueous solution (wherein, lanthanum chloride concentration is 0.04mol / L, and cerium chloride concentration is 0.06mol / L) mixing and beating, relative to 1L lanthanum chloride aqueous solution, the amount of molecular sieve after ammonium ion e...
PUM
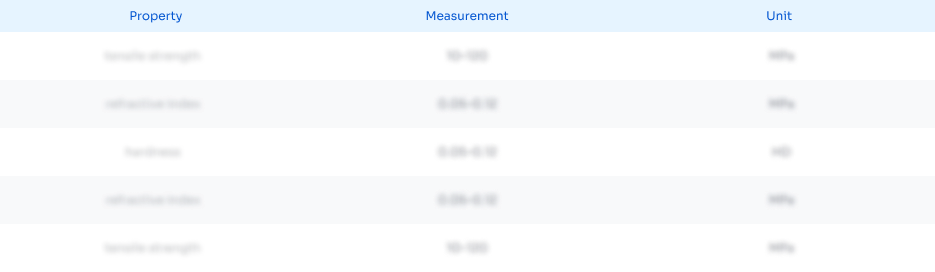
Abstract
Description
Claims
Application Information

- R&D
- Intellectual Property
- Life Sciences
- Materials
- Tech Scout
- Unparalleled Data Quality
- Higher Quality Content
- 60% Fewer Hallucinations
Browse by: Latest US Patents, China's latest patents, Technical Efficacy Thesaurus, Application Domain, Technology Topic, Popular Technical Reports.
© 2025 PatSnap. All rights reserved.Legal|Privacy policy|Modern Slavery Act Transparency Statement|Sitemap|About US| Contact US: help@patsnap.com