Method for controlling grain size of 1-series alloy cast-rolled plate in cast-rolling process
A technology of grain size and control method, which is applied in the field of aluminum alloy processing, can solve problems such as performance pinholes and grain growth, and achieve the effects of fine grain size, changing the degree of supercooling, and changing crystallization conditions
- Summary
- Abstract
- Description
- Claims
- Application Information
AI Technical Summary
Problems solved by technology
Method used
Image
Examples
Embodiment 1
[0041] A method for controlling the grain size of a 1070 alloy cast-rolled plate during casting and rolling, wherein the grain refinement comprises the following steps:
[0042] (s1) Increase the supercooling degree: control the metal purity of the 1 series alloy, the control percentage range is Si: 0.08%; Fe: 0.15%; Cu: 0.03-0.35%; Mn: 0.02%; Ti: 0.02-0.03%; Al : 99.7%;
[0043] (s2) Modification treatment: during the casting and rolling production process, a grain refiner is added before the crystallization of the aluminum melt, and the grain refiner is AlTi 3 and TiB 2 For aluminum titanium boron wire with a weight ratio of 1:1.5, the grain refiner is added at a rate of 0.03%% during the casting and rolling process; the melt temperature is controlled at 700°C during the smelting process;
[0044] (s3) Vibration and stirring: In the casting and rolling area, the solidified aluminum plate is rotated and rolled by the casting roll to break the grains; the control parameters ...
Embodiment 2
[0046] A method for controlling the grain size of a 1060 alloy cast-rolled plate during casting and rolling, wherein the grain refinement comprises the following steps:
[0047] (s1) Increase the supercooling degree: control the metal purity of the 1 series alloy, the control percentage range is Si: 0.08%; Fe: 0.18%; Cu: 0.03-0.35%; Mn: 0.02%; Ti: 0.02-0.03%; Al : 99.6%;
[0048] (s2) Modification treatment: during the casting and rolling production process, a grain refiner is added before the crystallization of the aluminum melt, and the grain refiner is AlTi 3 and TiB 2 Aluminum-titanium-boron wire with a weight ratio of 1:1.5, the addition ratio of the grain refiner in the casting and rolling process is 0.05%; the melt temperature is controlled at 760°C during the smelting process;
[0049] (s3) Vibration and stirring: In the casting and rolling area, the solidified aluminum plate is rotated and rolled by the casting roll to break the grains; the control parameters are th...
Embodiment 3
[0051] A method for controlling grain size during casting and rolling of 1145 alloy cast rolling plate, wherein the grain refinement comprises the following steps:
[0052] (s1) Increase the supercooling degree: control the metal purity of the 1 series alloy, the control percentage range is Si: 0.15-0.19%; Fe: 0.40-0.45%; Cu: 0.02-0.04%; Mn: 0.02%; Ti: 0.02- 0.03%; Al: 99.45%;
[0053] (s2) Modification treatment: during the casting and rolling production process, a grain refiner is added before the crystallization of the aluminum melt, and the grain refiner is AlTi 3 and TiB 2 Aluminum-titanium-boron wire with a weight ratio of 1:1.5, the addition ratio of the grain refiner in the casting and rolling process is 0.05%; the melt temperature is controlled at 730°C during the smelting process;
[0054] (s3) Vibration and stirring: In the casting and rolling area, the solidified aluminum plate is rotated and rolled by the casting roll to break the grains; the control parameters ...
PUM
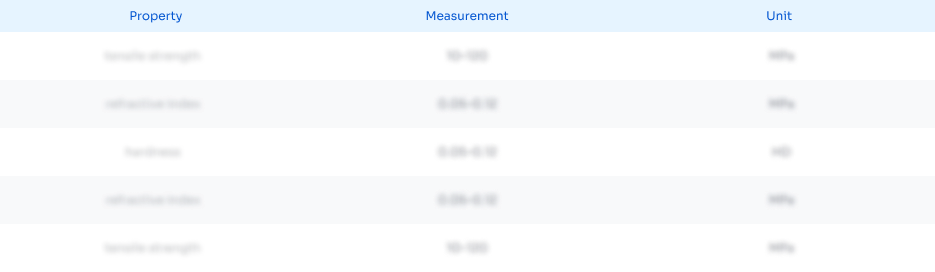
Abstract
Description
Claims
Application Information

- R&D Engineer
- R&D Manager
- IP Professional
- Industry Leading Data Capabilities
- Powerful AI technology
- Patent DNA Extraction
Browse by: Latest US Patents, China's latest patents, Technical Efficacy Thesaurus, Application Domain, Technology Topic, Popular Technical Reports.
© 2024 PatSnap. All rights reserved.Legal|Privacy policy|Modern Slavery Act Transparency Statement|Sitemap|About US| Contact US: help@patsnap.com