Continuous processing technology for improving fuzzing and pilling of dope-dyed fabric
A technology of pilling and dope coloring, which is applied in the field of textile printing and dyeing, can solve the problems of poor anti-pilling ability, affecting wearing performance, and has not been found to improve the anti-pilling of fabric dope coloring, etc., to achieve the improvement of pilling, pilling, Reduce the discharge of printing and dyeing wastewater and improve the hand feeling
- Summary
- Abstract
- Description
- Claims
- Application Information
AI Technical Summary
Problems solved by technology
Method used
Examples
Embodiment 1
[0029] Fabric: solution dyed polyester / viscose blended 40pcs*dope dyed polyester / viscose blended 40pcs*120*90, weave: 2 / 2S.
[0030] (1) singeing: speed: 120m / min, burning: 16mbar;
[0031] (2) Cold pile: caustic soda (48Be): 15g / L, hydrogen peroxide 27.5% (H 2 o 2 ): 5g / L, penetrant MAG-L: 12g / L, cold pile synergist BF 1631: 6g / L, stacking time: 24h, vehicle speed: 70m / min;
[0032] (3) Washing: washing tank temperature: 95°C, speed: 70m / min;
[0033] (4) Stenter: self-crosslinking polyether polyurethane FUN 6220: 30g / L, silicon softener DT-8500T: 20g / L, NA: 1.0g / L, HW: 1.5g / L, vehicle speed: 50m / L min, drying room temperature: 140°C.
[0034] (5) After finishing the fabric, the tested indicators are as follows:
[0035] ①Break strength: ASTM D5034-2009 test method, warp direction: 121Lb, weft direction: 93Lb;
[0036] ②Tear strength: ASTM D1424-2009 test method, warp direction: 8.5Lb, weft direction: 7.6Lb;
[0037] ③Pilling: ASTM D4970-2010 test method, level 3.5.
Embodiment 2
[0039] Fabric: solution-dyed polyester / viscose blended 40pcs*dope-dyed polyester / viscose blended 40pcs*210*140, weave: double layer.
[0040] (1) singeing: speed: 120m / min, burning: 16mbar;
[0041] (2) Cold pile: caustic soda (48Be): 15g / L, hydrogen peroxide 27.5% (H 2 o 2 ): 8g / L, penetrant MAG-L: 12g / L, cold pile synergist BF 1631: 8g / L, stacking time: 24h, vehicle speed: 70m / min;
[0042] (3) Washing: washing tank temperature: 95°C, speed: 70m / min;
[0043] (4) Stenter: self-crosslinking polyether polyurethane FUN 6220: 40g / L, silicon softener DT-8500T: 10g / L, NA: 1.0g / L, HW: 1.5g / L, vehicle speed: 50m / L min; drying room temperature: 140°C.
[0044] (5) After finishing the fabric, the tested indicators are as follows:
[0045] ①Break strength: ASTM D5034-2009 test method, warp direction: 203Lb, weft direction: 124Lb;
[0046] ②Tear strength: ASTM D1424-2009 test method, warp direction: 14Lb, weft direction: 14Lb;
[0047] ③Pilling: ASTM D4970-2010 test method, level...
Embodiment 3
[0049] Fabric: solution-dyed polyester / viscose blended 40*130*90, weave: DB16.
[0050] (1) singeing: speed: 120m / min, burning: 16mbar;
[0051] (2) Cold pile: caustic soda (48Be): 15g / L, hydrogen peroxide 27.5% (H 2 o 2 ): 8g / L, penetrant MAG-L: 12g / L, cold pile synergist BF 1631: 8g / L, stacking time: 24h, vehicle speed: 70m / min;
[0052] (3) Washing: washing tank temperature: 95°C, speed: 70m / min;
[0053] (4) Stenter: self-crosslinking polyether polyurethane FUN 6220: 50g / L, silicon softener DT-8500T: 30g / L, NA: 1.0g / L, HW: 1.5g / L, vehicle speed: 50m / L min; drying room temperature: 140°C.
[0054] (5) After finishing the fabric, the tested indicators are as follows:
[0055] ①Break strength: ASTM D5034-2009 test method, warp direction: 89Lb, weft direction: 72Lb;
[0056] ②Tear strength: ASTM D1424-2009 test method, warp direction: 6.2Lb, weft direction: 4.9Lb;
[0057] ③Pilling: ASTM D4970-2010 test method, level 3.5.
PUM
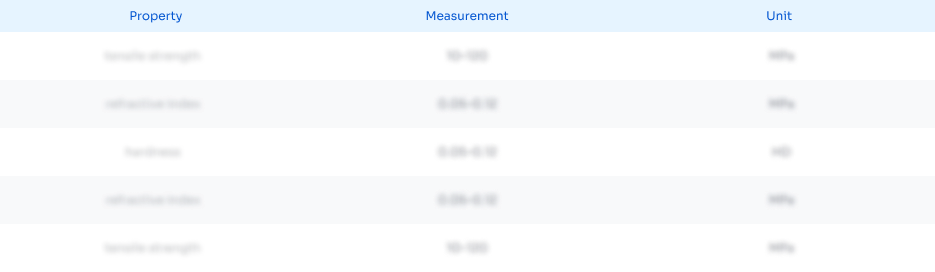
Abstract
Description
Claims
Application Information

- R&D
- Intellectual Property
- Life Sciences
- Materials
- Tech Scout
- Unparalleled Data Quality
- Higher Quality Content
- 60% Fewer Hallucinations
Browse by: Latest US Patents, China's latest patents, Technical Efficacy Thesaurus, Application Domain, Technology Topic, Popular Technical Reports.
© 2025 PatSnap. All rights reserved.Legal|Privacy policy|Modern Slavery Act Transparency Statement|Sitemap|About US| Contact US: help@patsnap.com