Efficient electric smelting magnesium lump waste heat recovery equipment and process
A waste heat recovery equipment and waste heat recovery technology, applied in the field of fused magnesia smelting, can solve the problems of low hot air temperature, waste of heat energy, deterioration of the surrounding environment, etc. Effect
- Summary
- Abstract
- Description
- Claims
- Application Information
AI Technical Summary
Problems solved by technology
Method used
Image
Examples
Embodiment Construction
[0016] The present invention will be further described below in conjunction with the accompanying drawings.
[0017] like figure 1 As shown, a high-efficiency electric fused magnesium lump waste heat recovery process and equipment, the equipment involved in the process flow includes No. 1 dust collector 3, material preheating tower 2, three-phase electric arc furnace 5, and No. 2 dust collector 4. Sealed shelling chamber 6, ferry trolley 7, waste heat recovery chamber 9, phase change heat storage material 10, phase change heat storage material shell 8, crushing device 11, high temperature heat exchange tower 12, blower 13, wherein the material is preheated The tower 2 is placed in front of the electric arc furnace 5, and the upper part of the electric arc furnace 5 is equipped with a No. 2 dust collector 4. The high-temperature flue gas generated during the smelting process is dedusted by the No. 2 dust collector 4 and used to produce dry ice. The shelling room is placed behin...
PUM
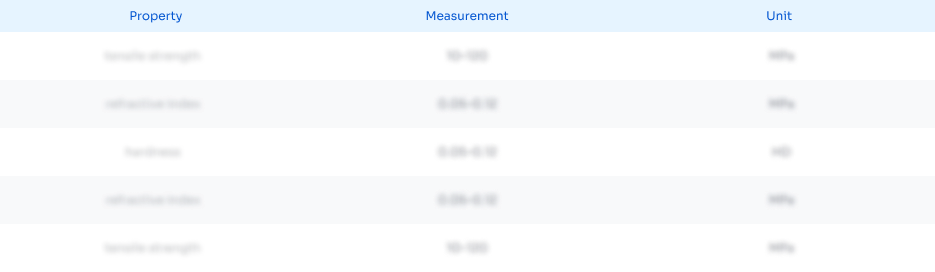
Abstract
Description
Claims
Application Information

- R&D
- Intellectual Property
- Life Sciences
- Materials
- Tech Scout
- Unparalleled Data Quality
- Higher Quality Content
- 60% Fewer Hallucinations
Browse by: Latest US Patents, China's latest patents, Technical Efficacy Thesaurus, Application Domain, Technology Topic, Popular Technical Reports.
© 2025 PatSnap. All rights reserved.Legal|Privacy policy|Modern Slavery Act Transparency Statement|Sitemap|About US| Contact US: help@patsnap.com