Regenerative environment-friendly yarn winding drum
A yarn winding and environmental protection technology, which is applied in the field of textile tools, can solve the problems of broken yarn winding tubes, etc., and achieve the effects of not easy to drop chips, realize recycling, and reduce pollution
- Summary
- Abstract
- Description
- Claims
- Application Information
AI Technical Summary
Problems solved by technology
Method used
Image
Examples
Embodiment 1
[0041] This embodiment discloses a regenerated ring winding bobbin, such as figure 1 As shown, it includes a bobbin main body 1 with several anti-slip stripes arranged at intervals on the outer surface, and the raw materials of the bobbin main body 1 include the following components in parts by weight: 80 parts of waste plastic particles, 6 parts of waste tire powder and 8 parts of waste car interiors EVA sheet.
[0042] The processing method of bobbin main body 1 comprises the steps:
[0043] S1. Mixing of raw materials; mixing and pulverizing waste plastic particles, waste tire powder and waste car interior EVA sheets, and blending to obtain a mixture;
[0044] S2. Injection molding: inject the mixture of S1 into a mold at 160° C. by an injection molding machine, and perform injection molding in four stages of filling, pressure maintaining, cooling, and demoulding to obtain the bobbin main body 1 .
Embodiment 2
[0046] This embodiment discloses a regenerated ring winding bobbin, such as figure 1 As shown, the bobbin main body 1 comprising several anti-slip stripes arranged at intervals on the outer surface, the raw material of the bobbin main body 1 includes the following components in parts by weight: 150 parts of waste plastic particles, 240 parts of waste tire powder and 340 parts of waste automobile interior trim EVA sheet.
[0047] The processing method of bobbin main body 1 comprises the steps:
[0048] S1. Mixing of raw materials; mixing and pulverizing waste plastic particles, waste tire powder and waste car interior EVA sheets, and blending to obtain a mixture;
[0049] S2. Injection molding: inject the mixture of S1 into a mold at 220° C. by an injection molding machine, and perform injection molding in four stages of filling, pressure holding, cooling, and demoulding to obtain the bobbin main body 1 .
Embodiment 3
[0051] This embodiment discloses a regenerated ring winding bobbin, such as figure 1 As shown, it includes a bobbin main body 1 with several anti-slip stripes arranged at intervals on the outer surface, and the raw materials of the bobbin main body 1 include the following components in parts by weight: 140 parts of waste plastic particles, 70 parts of waste tire powder and 140 parts of waste car interior trim EVA sheet.
[0052] The processing method of bobbin main body 1 comprises the steps:
[0053] S1. Mixing of raw materials; mixing and pulverizing waste plastic particles, waste tire powder and waste car interior EVA sheets, and blending to obtain a mixture;
[0054] S2. Injection molding: using an injection molding machine to inject the mixture of S1 into a mold at 200° C., and inject molding through four stages of filling, pressure maintaining, cooling, and demoulding to obtain the bobbin main body 1 .
PUM
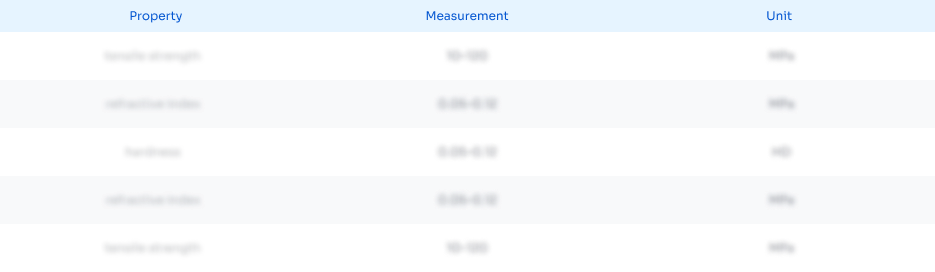
Abstract
Description
Claims
Application Information

- R&D
- Intellectual Property
- Life Sciences
- Materials
- Tech Scout
- Unparalleled Data Quality
- Higher Quality Content
- 60% Fewer Hallucinations
Browse by: Latest US Patents, China's latest patents, Technical Efficacy Thesaurus, Application Domain, Technology Topic, Popular Technical Reports.
© 2025 PatSnap. All rights reserved.Legal|Privacy policy|Modern Slavery Act Transparency Statement|Sitemap|About US| Contact US: help@patsnap.com