Method for removing silicon in lutetium yttrium silicate lixivium
A technology of yttrium lutetium silicate and leaching solution is applied in the field of rare earth recovery, which can solve the problems of ineffective removal and high silicon impurity content, and achieve the effects of shortening washing time, high rare earth yield and good economic benefits
- Summary
- Abstract
- Description
- Claims
- Application Information
AI Technical Summary
Problems solved by technology
Method used
Image
Examples
Embodiment 1
[0023] A method for removing silicon in yttrium lutetium silicate leaching solution, comprising the following steps:
[0024] (1) Take yttrium lutetium silicate waste and mix evenly with caustic soda to obtain mixture A, the mass ratio of yttrium lutetium silicate waste to caustic soda is 1:1.5, roast mixture A at 600°C for 6h, and then Mixture A was cooled to 70°C and placed in a reaction vessel, then 450mL of hot water was added to 100g of mixture A for mixing, then stirred and reacted at 105°C for 3.5h, and then filtered to obtain a rare earth hydroxide precipitate;
[0025] (2) Wash the rare earth hydroxide precipitate obtained in step (1) twice with sodium hydroxide solution; during each wash, the mass ratio of the rare earth hydroxide precipitate to the sodium hydroxide solution is 1g:32mL, and the hydroxide The sodium solution is mixed with the rare earth hydroxide precipitate and stirred at 45°C for 15 minutes at a stirring speed of 200r / min, then left to clarify, and ...
Embodiment 2
[0030] A method for removing silicon in yttrium lutetium silicate leaching solution, comprising the following steps:
[0031](1) Take yttrium lutetium silicate waste and mix evenly with caustic soda to obtain mixture A, the mass ratio of yttrium lutetium silicate waste to caustic soda is 1:1.5, roast mixture A at 600°C for 6h, and then Mixture A was cooled to 60°C and placed in a reaction vessel, then 400mL of hot water was added to 100g of mixture A for mixing, then stirred and reacted at 100°C for 3h, and then filtered to obtain rare earth hydroxide precipitates;
[0032] (2) Wash the rare earth hydroxide precipitate obtained in step (1) twice with sodium hydroxide solution; during each wash, the mass ratio of the rare earth hydroxide precipitate to the sodium hydroxide solution is 1g:30mL, and the hydroxide The sodium solution is mixed with the rare earth hydroxide precipitate and stirred at 40°C for 10 minutes at a stirring speed of 100 r / min, then left to clarify, and the...
Embodiment 3
[0037] A method for removing silicon in yttrium lutetium silicate leaching solution, comprising the following steps:
[0038] (1) Take yttrium lutetium silicate waste and mix evenly with caustic soda to obtain mixture A, the mass ratio of yttrium lutetium silicate waste to caustic soda is 1:1.5, roast mixture A at 600°C for 6h, and then Mixture A was cooled to 75°C and placed in a reaction vessel, then 480mL of hot water was added to each 100g of mixture A for mixing, then stirred and reacted at 105°C for 3.5h, and then filtered to obtain a rare earth hydroxide precipitate;
[0039] (2) Wash the rare earth hydroxide precipitate obtained in step (1) with sodium hydroxide solution for 3 times; during each washing, the mass ratio of the rare earth hydroxide precipitate to the sodium hydroxide solution is 1g:33mL, and the hydroxide The sodium solution is mixed with the rare earth hydroxide precipitate and stirred at 48°C for 12 minutes at a stirring speed of 200r / min, then left to...
PUM
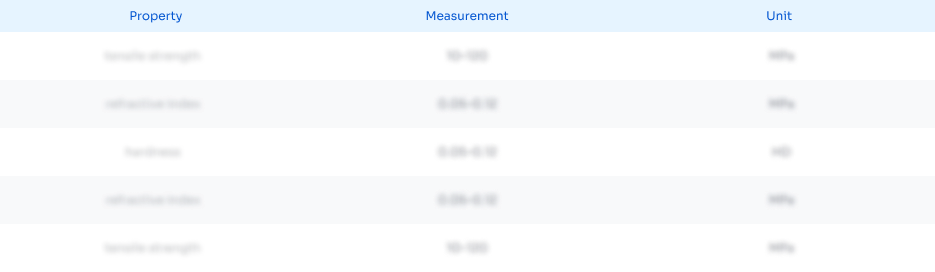
Abstract
Description
Claims
Application Information

- R&D Engineer
- R&D Manager
- IP Professional
- Industry Leading Data Capabilities
- Powerful AI technology
- Patent DNA Extraction
Browse by: Latest US Patents, China's latest patents, Technical Efficacy Thesaurus, Application Domain, Technology Topic, Popular Technical Reports.
© 2024 PatSnap. All rights reserved.Legal|Privacy policy|Modern Slavery Act Transparency Statement|Sitemap|About US| Contact US: help@patsnap.com