Preparation method of lactide
A technology of lactide and lactic acid, which is applied in the direction of organic chemistry, can solve the problems of low molecular weight of polymerization products, high polymerization reaction temperature, and poor mechanical properties of products, so as to reduce production costs, reduce cracking temperature, and improve production efficiency. Effect
- Summary
- Abstract
- Description
- Claims
- Application Information
AI Technical Summary
Problems solved by technology
Method used
Image
Examples
Embodiment 1
[0034] 1.1 Heat 180g of lactic acid, 40g of PEG400, 1.34g of dimethylolpropionic acid and 0.5g of stannous chloride into a round-bottomed flask in sequence, rapidly raise the temperature of the flask to 150°C and stir the reactants while collecting the reaction Generated water, when no liquid distilled out from the reaction, was vacuumized for polycondensation reaction. After 10 hours, the oligomerization reaction was completed to obtain 140 g of oligomeric lactic acid, and the molecular weight of oligomeric lactic acid was 3800 g / mol as measured by sampling.
[0035] 1.2 Mix the oligomeric lactic acid and 1 g of antimony trioxide in Example 1.1 and heat them to 190 degrees, vacuumize and carry out the cracking reaction. During the cracking reaction, continuously fill in nitrogen gas. When the cracking product no longer distills out, it is regarded as The reaction was completed, the reaction time was 1.5 h, and the yield was 96%. The lactide obtained in the present embodiment ...
Embodiment 2
[0039] 2.1 Heat 180g of lactic acid, 80g of PEG400, 5.28g of glyceric acid and 0.6g of stannous benzoate into the round-bottomed flask in turn, rapidly raise the temperature of the flask to 160 degrees Celsius and stir the reactants, while collecting the water generated by the reaction , when the reaction no longer has liquid distilling out, vacuumize the polycondensation reaction, after 8 hours, the oligomerization reaction ends, and the molecular weight of oligomeric lactic acid measured by sampling is 4100g / mol.
[0040] 2.2 Mix and heat the oligomeric lactic acid and 0.5g stannous benzoate in Example 2.1 to 180 degrees, vacuumize and carry out the cracking reaction, constantly charge nitrogen gas during the cracking reaction, when the cracking product no longer distills out, depending on To complete the reaction, the reaction time was 2h, and the yield was 95%. The purity of lactide measured by sampling was 97.2%, and the acid value was 22ppm.
Embodiment 3
[0042] 3.1 Heat 180g of lactic acid, 60g of PEG600, 4.02g of dimethylolpropionic acid and 0.9g of stannous octoate into a round-bottomed flask in turn, rapidly raise the temperature of the flask to 140 degrees Celsius and stir the reactants, and collect the reaction products at the same time Water, when the reaction no longer has liquid to distill, vacuumize and carry out the polycondensation reaction, after 12 hours, the oligomerization reaction ends, and the molecular weight of the oligomeric lactic acid measured by sampling is 3500g / mol.
[0043] 3.2 Mix and heat the oligomeric lactic acid and 0.5 g of stannous octoate in Example 3.1 to 190 degrees, vacuumize and carry out the cracking reaction, and constantly fill in nitrogen gas during the cracking reaction, and when the cracking product no longer distills out, depending on To complete the reaction, the reaction time is 1.5 h, and the yield is 96.5%. The purity of lactide measured by sampling was 97.3%, and the acid value...
PUM
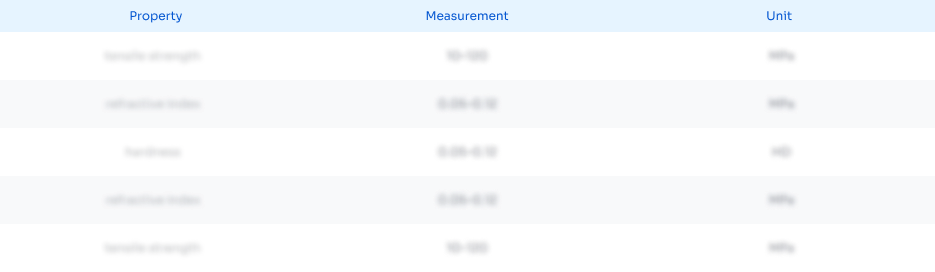
Abstract
Description
Claims
Application Information

- Generate Ideas
- Intellectual Property
- Life Sciences
- Materials
- Tech Scout
- Unparalleled Data Quality
- Higher Quality Content
- 60% Fewer Hallucinations
Browse by: Latest US Patents, China's latest patents, Technical Efficacy Thesaurus, Application Domain, Technology Topic, Popular Technical Reports.
© 2025 PatSnap. All rights reserved.Legal|Privacy policy|Modern Slavery Act Transparency Statement|Sitemap|About US| Contact US: help@patsnap.com