Centrifugal machine for processing aluminum silicate fiber heat preservation cotton
An aluminum silicate fiber and centrifuge technology, applied in the field of centrifuges, can solve the problems of easy failure of the spinning machine, affecting the spinning effect, uneven melt, etc., so as to improve the service life, increase the output, and improve the spinning The effect of silk fiber formation
- Summary
- Abstract
- Description
- Claims
- Application Information
AI Technical Summary
Problems solved by technology
Method used
Image
Examples
Embodiment 1
[0027] See attached Figure 1-5 As shown, it includes two centrifuges arranged side by side on the base 2. It is characterized in that the centrifuge includes a centrifuge body 1, a walking mechanism, and a first connecting plate 201 and a second connecting plate 202 that are spaced up and down and are horizontally arranged. , the second connecting plate 202 is provided with a running mechanism for driving the second connecting plate 202 to move back and forth on the track provided on the base 2, the running mechanism is connected with the second connecting plate 202 through the second shock absorbing mechanism 4, and the second connecting The plate 202 is connected to the first connecting plate 201 through the first damping mechanism 3 , and the first connecting plate 201 is connected to the centrifuge body 1 through the angle adjusting mechanism 8 .
[0028] When it is necessary to use the centrifuge body 1 to process the fiber insulation cotton, the angle adjustment mechani...
Embodiment 2
[0042] The difference between embodiment 2 and embodiment 1 is that in embodiment 2, a single or multiple resistance furnaces can be installed above the two centrifuge bodies 1, and the position and resistance of the resistance furnace can be set according to the use of the centrifuge body 1. For the flow direction of the melt in the furnace, the two centrifuge bodies 1 can be used alone, at the same time, or in combination.
[0043] When the centrifuge body 1 breaks down or needs to be overhauled, another set of centrifuge body 1 can be used to ensure that the melt in the resistance furnace is poured into the centrifuge body 1 for work, thereby improving work efficiency.
[0044] When two centrifuge bodies 1 need to be used at the same time, it is ensured that the centrifuge bodies 1 are used at the same time, which improves the work efficiency and increases the output.
[0045] When the two sets of centrifuge bodies 1 need to be used in combination, the positions of the two ...
PUM
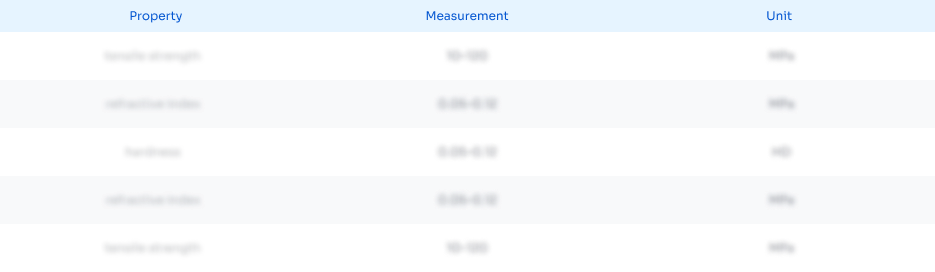
Abstract
Description
Claims
Application Information

- Generate Ideas
- Intellectual Property
- Life Sciences
- Materials
- Tech Scout
- Unparalleled Data Quality
- Higher Quality Content
- 60% Fewer Hallucinations
Browse by: Latest US Patents, China's latest patents, Technical Efficacy Thesaurus, Application Domain, Technology Topic, Popular Technical Reports.
© 2025 PatSnap. All rights reserved.Legal|Privacy policy|Modern Slavery Act Transparency Statement|Sitemap|About US| Contact US: help@patsnap.com