High-performance rotational molding product cross-linking foaming molding process
A molding process and high-performance technology, which is applied in the field of cross-linking foam molding of high-performance rotomolding products to achieve the effects of strong impact resistance, high plasticity and easy operation.
- Summary
- Abstract
- Description
- Claims
- Application Information
AI Technical Summary
Problems solved by technology
Method used
Examples
Embodiment 1
[0015] A cross-linked foam molding process for high-performance rotomolded products, comprising the following steps:
[0016] S1. Mold selection, select the required mold, a space for placing materials is formed inside the mold, and the upper part is in the shape of an opening, and the mold is fixed in the heating chamber.
[0017] S2. The plastic plate is crushed and ground with a grinder until it is ground into plastic powder, and set aside for later use. The plastic powder is 20 mesh.
[0018] S3. Introduce the plastic powder in S2 into the material placement space in the mold in S1, close the mold, fix the peripheral wall of the mold, and open a feeding slot on the upper part of the mold.
[0019] S4. The temperature in the heating chamber in S1 is raised to 40° C., and a stabilizer and a catalyst are added to the feeding slot on the upper part of the mold in S3. The catalyst is an alkali metal compound, and the stabilizer is hydroxybenzophenone. Stir with a stirrer, and t...
Embodiment 2
[0023] A cross-linked foam molding process for high-performance rotomolded products, comprising the following steps:
[0024] S1. Mold selection, select the required mold, a space for placing materials is formed inside the mold, and the upper part is in the shape of an opening, and the mold is fixed in the heating chamber.
[0025] S2. The plastic plate is crushed and ground with a grinder, and ground to plastic powder, which is set aside, and the plastic powder is 50 mesh.
[0026] S3. Introduce the plastic powder in S2 into the material placement space in the mold in S1, close the mold, fix the peripheral wall of the mold, and open a feeding slot on the upper part of the mold.
[0027] S4. Raise the temperature in the heating chamber in S1 to 45°C, add a stabilizer and a catalyst to the feeding slot on the upper part of the mold in S3, the catalyst is an alkali metal compound, and the stabilizer is hydroxybenzophenone. Stir with a mixer. The rotation speed is 13r / min until ...
Embodiment 3
[0031] A cross-linked foam molding process for high-performance rotomolded products, comprising the following steps:
[0032] S1. Mold selection, select the required mold, a space for placing materials is formed inside the mold, and the upper part is in the shape of an opening, and the mold is fixed in the heating chamber.
[0033] S2. The plastic plate is crushed and ground by a grinder until it is ground to plastic powder, which is set aside, and the plastic powder is 80 mesh.
[0034] S3. Introduce the plastic powder in S2 into the material placement space in the mold in S1, close the mold, fix the peripheral wall of the mold, and open a feeding slot on the upper part of the mold.
[0035] S4. Raise the temperature in the heating chamber in S1 to 50°C, add a stabilizer and a catalyst to the feeding slot on the upper part of the mold in S3, the catalyst is an alkali metal compound, and the stabilizer is hydroxybenzophenone. Stir with a mixer. The rotation speed is 16r / min u...
PUM
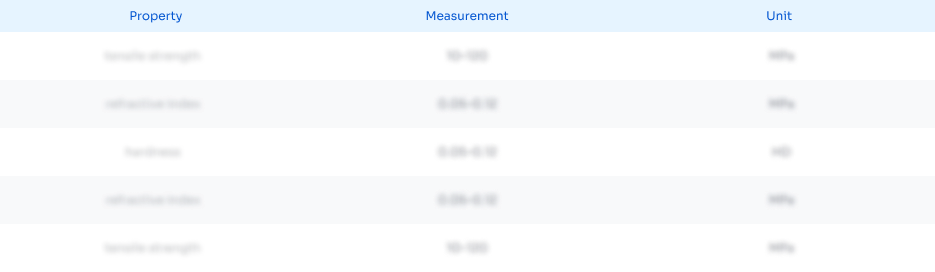
Abstract
Description
Claims
Application Information

- Generate Ideas
- Intellectual Property
- Life Sciences
- Materials
- Tech Scout
- Unparalleled Data Quality
- Higher Quality Content
- 60% Fewer Hallucinations
Browse by: Latest US Patents, China's latest patents, Technical Efficacy Thesaurus, Application Domain, Technology Topic, Popular Technical Reports.
© 2025 PatSnap. All rights reserved.Legal|Privacy policy|Modern Slavery Act Transparency Statement|Sitemap|About US| Contact US: help@patsnap.com