Processing technology of flange cover plate
A processing technology, flange cover technology, applied in the direction of metal processing equipment, forming tools, manufacturing tools, etc., can solve the problems of high processing cost and difficult processing, achieve precise size control, improve production efficiency, and increase yield Effect
- Summary
- Abstract
- Description
- Claims
- Application Information
AI Technical Summary
Problems solved by technology
Method used
Image
Examples
Embodiment Construction
[0050] The present invention will be described in further detail below in conjunction with the accompanying drawings.
[0051] The invention discloses a processing technology of a flange cover plate. The processing technology is applied to the processing of the cover plate and is suitable for processing and forming flange-type right-angle cover plates. After the processing and forming, the finished side wall of the finished cover plate 1 The minimum radius of the fillet at the vertical junction between 102 and the finished bottom plate 101 can reach 0.5mm, which is more than four times smaller than the minimum radius of traditional forming.
[0052] The whole processing technology is generally divided into two stages, namely the blanking stage and the forming stage. In the blanking stage, the cover plate 2 to be processed is obtained. The cover plate 2 to be processed is circular, and the processing allowance has been reserved in advance for the cover plate 2 to be processed. ...
PUM
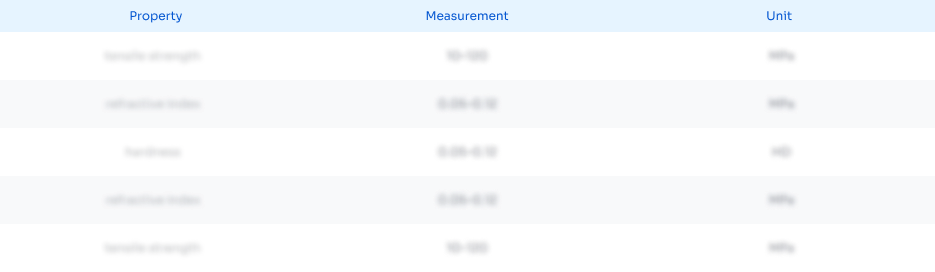
Abstract
Description
Claims
Application Information

- R&D Engineer
- R&D Manager
- IP Professional
- Industry Leading Data Capabilities
- Powerful AI technology
- Patent DNA Extraction
Browse by: Latest US Patents, China's latest patents, Technical Efficacy Thesaurus, Application Domain, Technology Topic, Popular Technical Reports.
© 2024 PatSnap. All rights reserved.Legal|Privacy policy|Modern Slavery Act Transparency Statement|Sitemap|About US| Contact US: help@patsnap.com