Method for adjusting rotational inertia of inertia friction welding
A friction welding and moment of inertia technology, applied in the field of inertia friction welding, can solve the problems of equipment accuracy and dynamic balance damage, major damage to the spindle and drive motor, and inability to meet welding needs, reducing welding quality and ensuring continuity and smoothness. performance, ensuring welding efficiency and welding quality
- Summary
- Abstract
- Description
- Claims
- Application Information
AI Technical Summary
Problems solved by technology
Method used
Image
Examples
Embodiment
[0038] Such as Figure 1-8 As shown, a method for adjusting the moment of inertia of inertial friction welding is characterized in that: a flywheel adjustment device is used for welding, and the flywheel adjustment device includes a device body 10, a drive motor 20, a first gear 30, a second gear 40, and a second gear 40. Three gears 50, lead screw clutch 60, fourth gear 70, fifth gear 80, lead screw 90, main shaft clutch 100, main shaft 110, conical flywheel disc 120, mass slider 130, connecting rod 140 and connecting member 150; device The body 10 includes a supporting platform 11, a gear bracket 12, a clutch bracket 13, a rotating shaft bracket 14, a screw bracket 15 and a main shaft bracket 16; the upper end surface of the supporting platform 11 is from left to right (such as figure 1 , figure 2 As shown), the gear bracket 12, the clutch bracket 13, the rotating shaft bracket 14, the screw bracket 15 and the main shaft bracket 16 are fixedly arranged in sequence; the out...
PUM
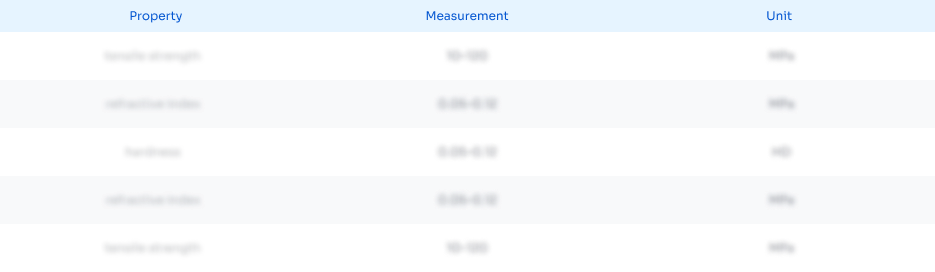
Abstract
Description
Claims
Application Information

- R&D
- Intellectual Property
- Life Sciences
- Materials
- Tech Scout
- Unparalleled Data Quality
- Higher Quality Content
- 60% Fewer Hallucinations
Browse by: Latest US Patents, China's latest patents, Technical Efficacy Thesaurus, Application Domain, Technology Topic, Popular Technical Reports.
© 2025 PatSnap. All rights reserved.Legal|Privacy policy|Modern Slavery Act Transparency Statement|Sitemap|About US| Contact US: help@patsnap.com