Production process method of PCB
A production process and PCB board technology, applied in the field of PCB board production process, can solve the problems of high production cost and environmental pollution, and achieve the effect of increasing income, reducing production cost and improving working environment
- Summary
- Abstract
- Description
- Claims
- Application Information
AI Technical Summary
Problems solved by technology
Method used
Image
Examples
Embodiment 1
[0035] The present embodiment provides a kind of production technology method of PCB board, specifically comprises the following steps:
[0036] S1. Pre-printing treatment of the single panel: Use dilute sulfuric acid with a mass concentration of 5% to pickle the surface of the typesetting and cutting single panel, then wash it with water, and then use a 600-mesh nylon brush for grinding treatment, wash with water Finally, dry at 90°C;
[0037] S2. The side of the single-sided panel with copper foil is printed with solder resist ink to print the circuit pattern: use Guangxin green oil to print the circuit pattern on the surface of the pre-treated single-sided panel. The ink thickness of the circuit pattern is 15 μm, and then the circuit pattern is printed. Bake the single panel at 150°C for 30 minutes;
[0038] S3. Text printing on the other side of the single-sided board, that is, the substrate side: use white text ink to print text on the other side of the printed circuit g...
Embodiment 2
[0043] This embodiment provides a production process for PCB boards. The only difference from Embodiment 1 is that the concentration of sulfuric acid in the electrolyte used in the S4 step is 180g / L, the concentration of copper sulfate is 70g / L, and the concentration of chloride ions is 80ppm, and the pH of the electrolyte is 5.0.
[0044] The good product rate of the PCB board prepared by the method of this embodiment is 99.5%.
Embodiment 3
[0046] This embodiment provides a production process for PCB boards. The only difference from Embodiment 1 is that the concentration of sulfuric acid in the electrolyte used in the S4 step is 180g / L, the concentration of copper sulfate is 70g / L, and the concentration of chloride ions is 60ppm, and the pH of the electrolyte is 4.0.
[0047] The good product rate of the PCB board prepared by the method of this embodiment is 99.6%.
PUM
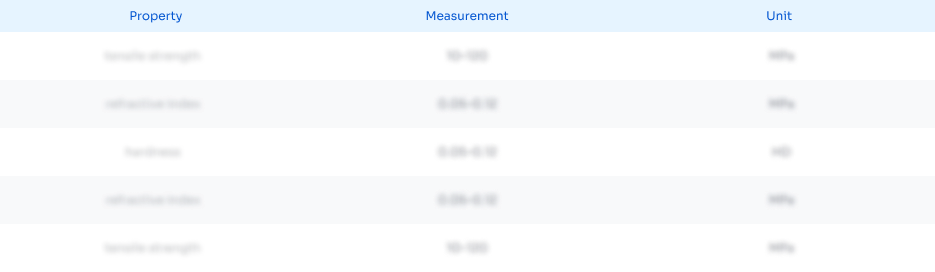
Abstract
Description
Claims
Application Information

- R&D
- Intellectual Property
- Life Sciences
- Materials
- Tech Scout
- Unparalleled Data Quality
- Higher Quality Content
- 60% Fewer Hallucinations
Browse by: Latest US Patents, China's latest patents, Technical Efficacy Thesaurus, Application Domain, Technology Topic, Popular Technical Reports.
© 2025 PatSnap. All rights reserved.Legal|Privacy policy|Modern Slavery Act Transparency Statement|Sitemap|About US| Contact US: help@patsnap.com