Preparation method and preparation device of electronic-grade dimethyl carbonate
A dimethyl carbonate and preparation device technology, applied in the purification/separation of carbonate/haloformate, general layout of crystallization device, crystallization adjustment/control, etc., can solve high energy consumption and reduce process safety To achieve the effects of high product purity, low energy consumption per unit product, and insensitivity to fluctuations in raw materials
- Summary
- Abstract
- Description
- Claims
- Application Information
AI Technical Summary
Problems solved by technology
Method used
Image
Examples
preparation example Construction
[0065] A kind of preparation method and device of electronic grade dimethyl carbonate, such as figure 1 As shown, the crude DMC product containing 95-99.5 wt% DMC is first stored in the raw material tank 51, and then pumped into the suspension crystallizer 1 for suspension crystallization. Suspension crystallization uses ethylene glycol aqueous solution as a refrigerant (cooling medium), enters the jacket of the suspension crystallizer 1, and controls the temperature of the materials in the suspension crystallizer 1. The material temperature in the suspension crystallizer 1 is set at -5~3.5°C, preferably -4~3°C, more preferably -3.5~2.8°C; the stirring speed is set at 10~30rpm, preferably 15~25rpm, more preferably 18°C ~25rpm; the temperature difference between the inlet temperature of the refrigerant and the material temperature in the suspension crystallizer 1 is 4~15°C, preferably 6~13°C, more preferably 7~12°C; the temperature difference between the inlet and outlet of the...
Embodiment 1
[0073] Using dimethyl carbonate produced by a certain process as a raw material, the content of dimethyl carbonate is 99.5wt%, the moisture content is 460ppm, and the methanol content is 0.4wt%. The remaining components are easily separated components, which are not listed here. .
[0074] Above-mentioned raw material first enters in suspension crystallizer 1 and carries out cooling crystallization, and crystallization material temperature is-2 ℃, and the stirring speed in suspension crystallizer 1 is 22rpm, and the inlet temperature of ethylene glycol aqueous solution in the suspension crystallizer 1 jacket is-8.3 ℃, The temperature difference between the ethylene glycol aqueous solution entering and leaving the jacket of the suspension crystallizer 1 is 0.5° C., and the solid content in the suspension crystallizer 1 is 31 wt%. Adopt vacuum drum filter (solid-liquid separator 2) to carry out solid-liquid separation to the slurry that is obtained by suspension crystallizer 1, ...
Embodiment 2
[0079] Dimethyl carbonate produced by a certain process is used as raw material, wherein the content of dimethyl carbonate is 95.7wt%, the moisture content is 0.7wt%, the methanol content is 2.9wt%, and the remaining components are easily separated components, which are not listed here. listed.
[0080] Above-mentioned raw material first enters in suspension crystallizer 1 and carries out cooling crystallization, and crystallization material temperature is-3 ℃, and the stirring speed in suspension crystallizer 1 is 20rpm, and the inlet temperature of ethylene glycol aqueous solution in suspension crystallizer 1 jacket is-13 ℃, The temperature difference between the ethylene glycol aqueous solution entering and leaving the jacket of the suspension crystallizer 1 is 0.6° C., and the solid content in the suspension crystallizer 1 is 29.6 wt%. Adopt horizontal multistage pusher centrifuge (solid-liquid separator 2) to carry out solid-liquid separation to the slurry that is obtaine...
PUM
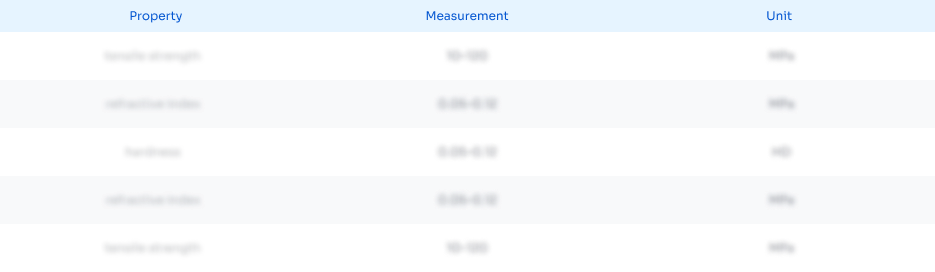
Abstract
Description
Claims
Application Information

- Generate Ideas
- Intellectual Property
- Life Sciences
- Materials
- Tech Scout
- Unparalleled Data Quality
- Higher Quality Content
- 60% Fewer Hallucinations
Browse by: Latest US Patents, China's latest patents, Technical Efficacy Thesaurus, Application Domain, Technology Topic, Popular Technical Reports.
© 2025 PatSnap. All rights reserved.Legal|Privacy policy|Modern Slavery Act Transparency Statement|Sitemap|About US| Contact US: help@patsnap.com