PMMA copolymerized functional resin and preparation method thereof
A functional resin and copolymerization technology, applied in the field of binary copolymer resin and its preparation, PMMA copolymerization functional resin and its preparation field, can solve the problems of large equipment investment, wider molecular weight distribution, and complicated post-processing.
- Summary
- Abstract
- Description
- Claims
- Application Information
AI Technical Summary
Problems solved by technology
Method used
Image
Examples
Embodiment 1
[0024] Methyl methacrylate accounting for 99.5% of the total amount of monomers, glycidyl methacrylate accounting for 0.5% of the total amount of monomers, all oil-soluble initiators azobisisobutyronitrile accounting for 0.3% of the total amount of monomers, All the molecular weight regulator dodecyl mercaptan accounting for 1% of the total monomer, all the dispersant active calcium phosphate accounting for 1.5% of the total monomer, and deionized water 1.5 times the total monomer weight were mixed in the reactor. Under normal stirring, react at 70°C for 3 hours, then raise the temperature to 95°C for aging for 1 hour; then discharge the material in the storage tank, filter and wash with deionized water, and then dry the obtained product at 90°C to constant weight to obtain the final Product PMMA functional copolymer resin.
[0025] figure 1 Be the infrared spectrum of the product PMMA copolymerization GMA functional resin of embodiment 1, at 1620~1680cm -1 There are no char...
Embodiment 2
[0027] Methyl methacrylate accounting for 90% of the total amount of monomers, glycidyl methacrylate accounting for 10% of the total amount of monomers, all oil-soluble initiator azobisisobutyronitrile accounting for 0.3% of the total amount of monomers, All the molecular weight regulator dodecyl mercaptan accounting for 1% of the total monomer, all the dispersant active calcium phosphate accounting for 1.5% of the total monomer, and deionized water 1.5 times the total monomer weight were mixed in the reactor. Under normal stirring, react at 70°C for 4 hours, then raise the temperature to 95°C and mature for 1 hour; then discharge the material into the storage tank, filter and wash with deionized water, and then dry the obtained product at 90°C to constant weight to obtain the final Product function Copolymer resin.
Embodiment 3
[0035] Methyl methacrylate accounting for 98% of the total amount of monomers, glycidyl methacrylate accounting for 2% of the total amount of monomers, all oil-soluble initiators azobisisobutyronitrile accounting for 0.35% of the total amount of monomers, All the molecular weight regulator dodecyl mercaptan accounting for 1% of the total monomer, all the dispersant active calcium phosphate accounting for 1.1% of the total monomer, and deionized water 1.5 times the total monomer weight were mixed in the reactor. React at 71°C for 3 hours under conventional stirring, then raise the temperature to 95°C for aging for 1 hour; then discharge the material into the storage tank, filter it conventionally and wash it with deionized water, and then dry the obtained product at 90°C to constant weight to obtain the final Product PMMA functional copolymer resin.
PUM
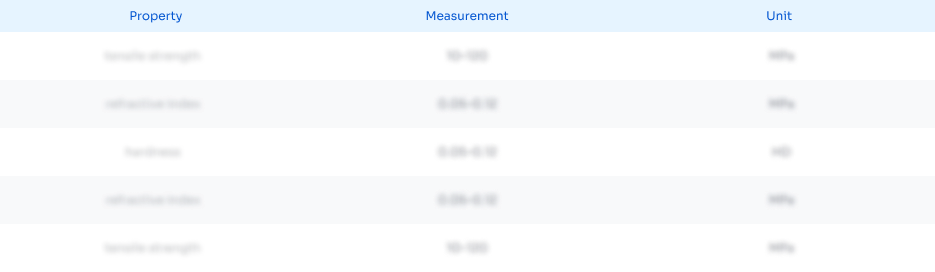
Abstract
Description
Claims
Application Information

- R&D Engineer
- R&D Manager
- IP Professional
- Industry Leading Data Capabilities
- Powerful AI technology
- Patent DNA Extraction
Browse by: Latest US Patents, China's latest patents, Technical Efficacy Thesaurus, Application Domain, Technology Topic, Popular Technical Reports.
© 2024 PatSnap. All rights reserved.Legal|Privacy policy|Modern Slavery Act Transparency Statement|Sitemap|About US| Contact US: help@patsnap.com