Electric melting plasma moment composite furnace device and method thereof for treating dangerous waste materials
A plasma moment and material technology, which is applied in the field of ion moment compound furnace device, can solve the problems of limited heating range, many harmful components, and large heat energy loss, so as to ensure the uniformity of material distribution, improve the processing efficiency, and ensure the bottom temperature.
- Summary
- Abstract
- Description
- Claims
- Application Information
AI Technical Summary
Problems solved by technology
Method used
Image
Examples
Embodiment 1
[0038] like Figures 1 to 3 As shown, an electric fusion plasma moment compound furnace device for processing hazardous waste materials includes an electrode 3 for heating the material at the bottom of the furnace body 1, and the electrode 3 is vertically movable on the furnace body 1, and it is placed The vertical linear drive mechanism 2 on one side of the furnace body 1 is driven up and down to adjust the distance between the bottom end of the electrode 3 and the bottom of the furnace body.
[0039] The vertical linear drive mechanism can be a cylinder, an oil cylinder, a lead screw module, a rack and pinion combination, a hoist, etc. In this embodiment, the vertical linear drive mechanism preferably adopts a lead screw module, and its housing is vertically fixed on the ground or other bearing platforms, and the driving slider threaded with the lead screw is connected to one end of the cross bar 11, and the The other end of the rod 11 is fixed on the vertical plate 12 , so...
Embodiment 2
[0044] like Figures 1 to 3 As shown, an electric fusion plasma moment compound furnace device for processing hazardous waste materials includes an electrode 3 for heating the material at the bottom of the furnace body 1, and the electrode 3 is vertically movable on the furnace body 1, and it is placed The vertical linear drive mechanism 2 on one side of the furnace body 1 is driven up and down to adjust the distance between the bottom end of the electrode 3 and the bottom of the furnace body. The feed inlet 4 of the furnace body 1 is arranged at the top center thereof. There are preferably three electrodes, which are distributed symmetrically along the center of the furnace body axis. The center of the furnace body 1 is equipped with a feed inlet, which can make the distribution of hazardous waste in the furnace body more uniform. Specifically, the feed inlet is located in the center of the three electrodes to ensure that the hot zone and the cold zone in the radial directio...
Embodiment 3
[0055] A method for processing hazardous waste materials, the method is implemented based on the device in any one of the above embodiments, which includes the following steps:
[0056] S1, put the hazardous waste materials to be processed into the furnace body 1;
[0057] S2. Start the vertical linear drive mechanism 2 to move the electrode 3 downward and insert it into the hazardous waste material, then stop the vertical linear drive mechanism 2;
[0058] S3, energize the electrode 3, and perform capacitive treatment of hazardous waste materials;
[0059] S4, start the vertical linear drive mechanism 2, so that the distance between the bottom of the electrode 3 and the top of the metal layer at the bottom of the hazardous waste heated to a molten state is L, and then stop the vertical linear drive mechanism 2;
[0060] S5, repeat step S4 regularly, keep the distance L between the electrode and the metal layer, until the metal in the metal layer is discharged;
[0061] S6. ...
PUM
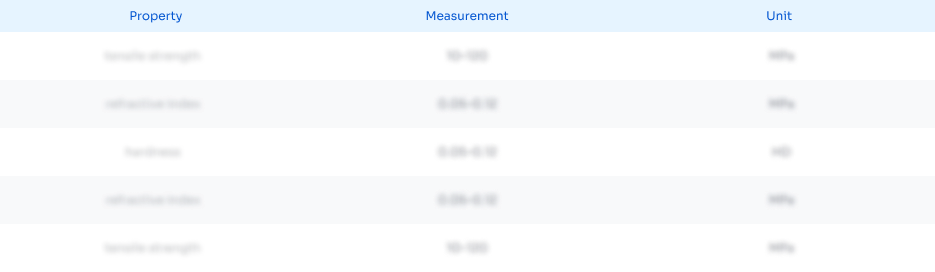
Abstract
Description
Claims
Application Information

- R&D
- Intellectual Property
- Life Sciences
- Materials
- Tech Scout
- Unparalleled Data Quality
- Higher Quality Content
- 60% Fewer Hallucinations
Browse by: Latest US Patents, China's latest patents, Technical Efficacy Thesaurus, Application Domain, Technology Topic, Popular Technical Reports.
© 2025 PatSnap. All rights reserved.Legal|Privacy policy|Modern Slavery Act Transparency Statement|Sitemap|About US| Contact US: help@patsnap.com