Preparation method of polypropylene foam
A polypropylene foam and foaming agent technology, applied in the field of polypropylene foam preparation, can solve the problems of weak toughness, difficulty in foaming polypropylene foam materials, and difficulty in dispersing nucleating agents, and achieves the effect of increasing toughness
- Summary
- Abstract
- Description
- Claims
- Application Information
AI Technical Summary
Problems solved by technology
Method used
Examples
preparation example Construction
[0017] In the embodiment of the present invention, a method for preparing polypropylene foam is characterized in that it includes the following steps: Step 1: Prepare the following materials according to the mass fraction ratio, including 90-100 parts of PP resin and 10-30 parts of foaming agent , 0.3-6 parts of foaming aids, 0.5-2 parts of crosslinking aids, 0.05-0.1 parts of antioxidants and 0.1-2 parts of nucleating agent precursors; step 2: first foaming aids The nucleating agent precursor is ground and sieved evenly, and finally the mixture is added to the mixer and mixed evenly; Step 3: Add PP resin, foaming agent, crosslinking agent, and antioxidant to the mixer in sequence for mixing, and finally mix the mixture Add a twin-screw extruder, use the twin-screw extruder to extrude and roll into thin sheets, and then foam to obtain polypropylene foam.
[0018] Further, a preparation method of polypropylene foam, the PP resin is a copolymerized PP resin; the foaming agent is...
Embodiment 1
[0022] First weigh 2 parts of pimelic acid and 2 parts of zinc oxide, grind them evenly and sieve them, then add them to the mixer, and mix 100 parts of PP resin, 20 parts of azodicarbonamide, 1 part of benzoyl peroxide, 0.08 parts Antioxidant 168 was sequentially added to the mixer, and mixed for 10 minutes at 120°C and 2MPa. After the mixture was obtained, the mixture was added to a twin-screw extruder at 150-190°C and rolled into sheets, and then foamed to obtain polypropylene foam.
Embodiment 2
[0024] First, weigh 0.1 part of adipic acid and 0.3 part of zinc oxide, grind them evenly and sieve them, then add them into the mixer, and mix 90 parts of PP resin, 10 parts of azodicarbonamide, 0.5 parts of dicumyl peroxide, 0.05 Parts of antioxidant 1010 were sequentially added to the mixer, and mixed at 150°C and 0.5MPa for 15 minutes to obtain a mixture, which was added to a twin-screw extruder at 150-190°C and rolled into sheets, and then foamed to obtain polypropylene foam.
PUM
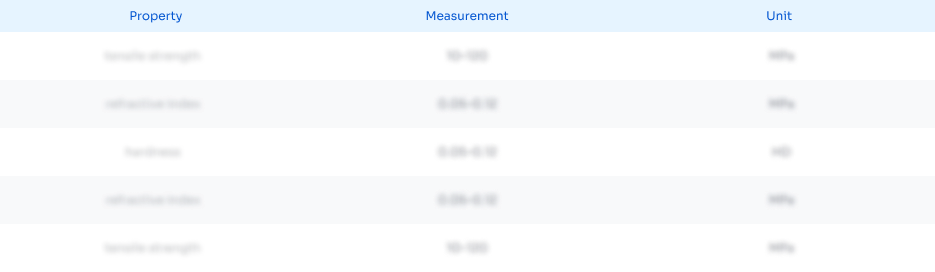
Abstract
Description
Claims
Application Information

- Generate Ideas
- Intellectual Property
- Life Sciences
- Materials
- Tech Scout
- Unparalleled Data Quality
- Higher Quality Content
- 60% Fewer Hallucinations
Browse by: Latest US Patents, China's latest patents, Technical Efficacy Thesaurus, Application Domain, Technology Topic, Popular Technical Reports.
© 2025 PatSnap. All rights reserved.Legal|Privacy policy|Modern Slavery Act Transparency Statement|Sitemap|About US| Contact US: help@patsnap.com