Precision die casting surface treatment device with damage repair function
A surface treatment device and damage repair technology, applied in the field of surface treatment devices for precision die-casting parts, can solve problems such as poor treatment effect, multiple dead angles, and internal stress concentration of die-casting parts, so as to improve repair stability, intelligently adjust repair amount, The effect of increasing the contact area
- Summary
- Abstract
- Description
- Claims
- Application Information
AI Technical Summary
Problems solved by technology
Method used
Image
Examples
Embodiment Construction
[0024] The following will clearly and completely describe the technical solutions in the embodiments of the present invention with reference to the accompanying drawings in the embodiments of the present invention. Obviously, the described embodiments are only some, not all, embodiments of the present invention. Based on the embodiments of the present invention, all other embodiments obtained by persons of ordinary skill in the art without making creative efforts belong to the protection scope of the present invention.
[0025] see Figure 1-9 , the present invention provides technical solutions:
[0026] Such as Figure 1-9 As shown, a precision die casting surface treatment device with damage repair function, including transfer assembly 1, surface treatment assembly 2, damage repair assembly 3, lower frame 4, transfer assembly 1, surface treatment assembly 2, damage repair assembly 3 and the upper surface of the lower frame 4 are firmly connected, and the transfer assembly...
PUM
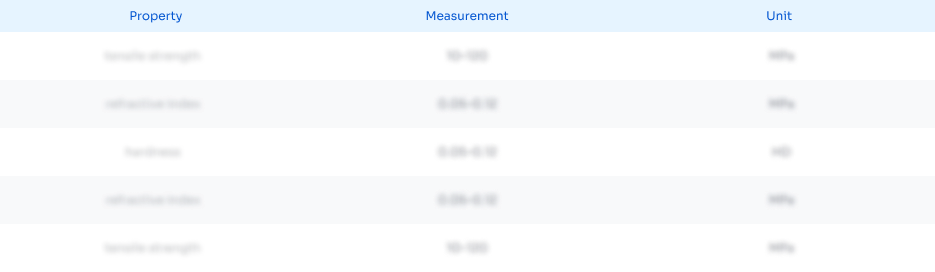
Abstract
Description
Claims
Application Information

- R&D
- Intellectual Property
- Life Sciences
- Materials
- Tech Scout
- Unparalleled Data Quality
- Higher Quality Content
- 60% Fewer Hallucinations
Browse by: Latest US Patents, China's latest patents, Technical Efficacy Thesaurus, Application Domain, Technology Topic, Popular Technical Reports.
© 2025 PatSnap. All rights reserved.Legal|Privacy policy|Modern Slavery Act Transparency Statement|Sitemap|About US| Contact US: help@patsnap.com