Preparation method of surface conductivity gradient coating for direct current GIL epoxy resin insulator
A technology of epoxy resin and surface conductivity, which is used in the manufacture of cables/conductors, insulators, conductive materials dispersed in non-conductive inorganic materials, etc. Effect
- Summary
- Abstract
- Description
- Claims
- Application Information
AI Technical Summary
Problems solved by technology
Method used
Image
Examples
preparation example Construction
[0037] A method for preparing a surface conductance gradient coating for DC GIL epoxy resin insulators, the method comprising the following steps: first divide the surface of the insulator into N parts from the high-voltage electrode to the ground electrode, and then divide the high-conductivity coating into N parts according to the conductivity from high to high It is coated on the surface of the insulator from the high-voltage electrode to the ground electrode in turn, and after curing, an insulator with a gradient distribution of gradually decreasing electrical conductivity is formed.
[0038] Wherein, the preparation method of high conductivity coating comprises the following steps:
[0039] S11. Preheat the epoxy resin, high conductivity filler, and curing agent at 80-90°C for 2-3 hours;
[0040] S12. Mix epoxy resin and high conductivity filler, heat and stir in an oil bath at 60-80°C for 25-35 minutes, keep the temperature, then add diluent, and continue stirring for 10...
Embodiment 1
[0055] A high conductivity coating is composed of the following raw materials according to mass percentage: E44 type epoxy resin 45%, TiO 2 5%, 650 polyamide ester 35%, acetone 10%, fumed silica 5%.
[0056] The preparation method of high conductivity paint comprises the steps:
[0057] S11, the E44 type epoxy resin, TiO 2 , 650 polyamide ester preheated at 80 ℃ for 2 hours;
[0058] S12, the E44 type epoxy resin and TiO 2 Mix, heat and stir in an oil bath at 60°C for 30 minutes, keep the temperature, then add acetone and continue stirring for 10 minutes to obtain mixture A;
[0059] S13. Add 650 polyamide ester and fumed silica to the mixture A prepared in step S12, and stir at room temperature for 10 minutes to obtain mixture B;
[0060] S14. Degas the mixture B prepared in step S13 in a vacuum environment at a temperature of 60° C. for 30 minutes to obtain a high-conductivity coating.
Embodiment 2
[0062] A high conductivity coating is composed of the following raw materials according to mass percentage: E44 type epoxy resin 42%, TiO 2 10%, 650 polyamide ester 33%, acetone 10%, fumed silica 5%.
[0063] The preparation method of high conductivity paint comprises the steps:
[0064] S11, the E44 type epoxy resin, TiO 2 , 650 polyamide ester preheated at 80 ℃ for 2 hours;
[0065] S12, the E44 type epoxy resin and TiO 2 Mix, heat and stir in an oil bath at 60°C for 30 minutes, keep the temperature, then add acetone and continue stirring for 10 minutes to obtain mixture A;
[0066] S13. Add 650 polyamide ester and fumed silica to the mixture A prepared in step S12, and stir at room temperature for 10 minutes to obtain mixture B;
[0067] S14. Degas the mixture B prepared in step S13 in a vacuum environment at a temperature of 60° C. for 30 minutes to obtain a high-conductivity coating.
PUM
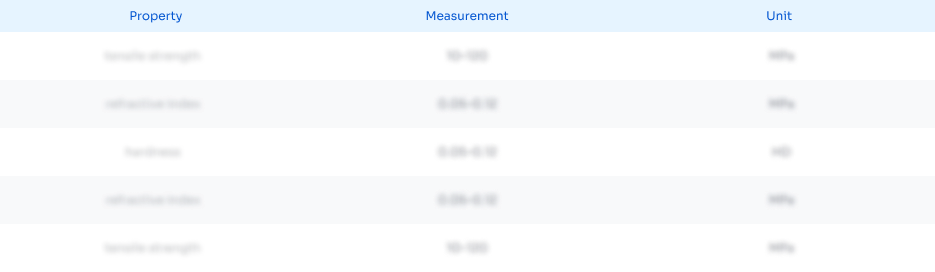
Abstract
Description
Claims
Application Information

- Generate Ideas
- Intellectual Property
- Life Sciences
- Materials
- Tech Scout
- Unparalleled Data Quality
- Higher Quality Content
- 60% Fewer Hallucinations
Browse by: Latest US Patents, China's latest patents, Technical Efficacy Thesaurus, Application Domain, Technology Topic, Popular Technical Reports.
© 2025 PatSnap. All rights reserved.Legal|Privacy policy|Modern Slavery Act Transparency Statement|Sitemap|About US| Contact US: help@patsnap.com