Thermal compounding manufacturing process of battery cell
A technology of thermal compounding and battery cells, which is applied in sustainable manufacturing/processing, manufacturing of electrolyte batteries, circuits, etc., can solve the problems of inability to guarantee the accuracy of positive and negative electrodes, consume a lot of time, and lack of alignment, so as to improve thermal compounding The effect of manufacturing process, reducing short-circuit flammability, and improving lamination efficiency
- Summary
- Abstract
- Description
- Claims
- Application Information
AI Technical Summary
Problems solved by technology
Method used
Image
Examples
Embodiment 1
[0041] Embodiment 1: as Figure 1 to Figure 3 As shown, the technical solution adopted in Embodiment 1 of the present invention is as follows: a manufacturing process of electric core thermal compounding, including the following process steps:
[0042] S1, the first pole piece is made: the first pole piece with a strip structure is formed by lug forming, and the pole piece is cut to form a single-piece first pole piece;
[0043] S2. Preparation of the second pole piece: the second pole piece with a band-shaped structure opposite to the polarity of the first pole piece in step S1 is formed by lug forming, and the pole piece is cut to form a single-piece second pole piece. ;
[0044] S3. Pole piece bag making: In step S1 or step S2, during the linear conveying process of the single-piece first pole piece or the second pole piece, the front and back sides are simultaneously covered with strip-shaped diaphragms, and the diaphragms on both sides are respectively connected to the s...
Embodiment 2
[0067] Embodiment 2: as Figure 4 As shown, it is a schematic diagram of the bag-making process flow in Embodiment 2 of the present invention. The production line in this embodiment and Embodiment 1 has the same components. The order is reversed, that is, after the surface thermal compounding process is completed, the diaphragm is cut along the middle of the distance between the adjacent two pole pieces. The contours are thermally laminated at the edges to form bags. The process of Example 1 is to first carry out edge heat compounding and then cut the continuous diaphragm. Since the continuous diaphragm is tensioned and there is internal stress, it is possible that after the edge heat compounding, the internal stress of the continuous diaphragm may cause pressure-swapping thermal compounding. The separation of layers of diaphragms after bonding is used as a replacement cell to make a production line and production process. In the process of this embodiment, the diaphragm is c...
PUM
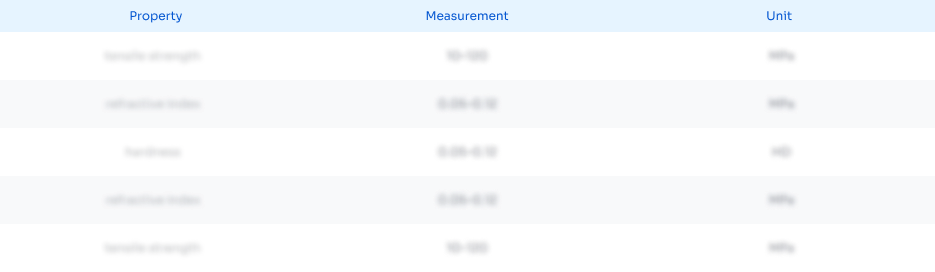
Abstract
Description
Claims
Application Information

- Generate Ideas
- Intellectual Property
- Life Sciences
- Materials
- Tech Scout
- Unparalleled Data Quality
- Higher Quality Content
- 60% Fewer Hallucinations
Browse by: Latest US Patents, China's latest patents, Technical Efficacy Thesaurus, Application Domain, Technology Topic, Popular Technical Reports.
© 2025 PatSnap. All rights reserved.Legal|Privacy policy|Modern Slavery Act Transparency Statement|Sitemap|About US| Contact US: help@patsnap.com