Sponge for shoes and production method of sponge
A production method and sponge technology, applied in the application, insole, footwear and other directions, can solve the problems of high hardness of rubber shoe sponge pad, insignificant cushioning effect, high foot fatigue, high foaming multiple, enhanced elasticity and toughness , the effect of good foam stability
- Summary
- Abstract
- Description
- Claims
- Application Information
AI Technical Summary
Problems solved by technology
Method used
Image
Examples
Embodiment 1
[0035] A sponge for shoes, comprising the following raw materials in parts by weight: 45 parts of toluene diisocyanate, 50 parts of polyether propylene glycol, 30 parts of polyether glycerol, 2.5 parts of triethylenediamine, 3.2 parts of triethylamine, and 3.6 parts of foaming agent parts, 6.5 parts of foam stabilizer, 1 part of catalyst, 8 parts of clam powder, 3 parts of sepiolite, and 2 parts of montmorillonite.
[0036] Wherein, the foam stabilizer is composed of zinc cyanurate, simethicone, sodium lauryl sulfate, glyceryl tristearate and triethanolamine in a ratio of 1:2:0.8:0.1:0.65 by weight.
[0037] The foaming agent consists of dichloromethane, petroleum ether, sodium lauryl sulfate, and trichlorofluoromethane in parts by weight 1:0.48:1.36:0.8.
[0038] The catalyst is composed of dibutyltin diacetate and stannous benzoate in a ratio of 1:1 in parts by mass.
[0039] Its production method comprises the following steps:
[0040] Step 1: Add polyether propylene glyc...
Embodiment 2
[0046] A sponge for shoes, comprising the following raw materials in parts by weight: 60 parts of toluene diisocyanate, 40 parts of polyether propylene glycol, 40 parts of polyether glycerol, 4.2 parts of triethylenediamine, 1.8 parts of triethylamine, and 5.2 parts of foaming agent 4.8 parts, 4.8 parts of foam stabilizer, 2 parts of catalyst, 5 parts of clam powder, 5 parts of sepiolite, 3 parts of montmorillonite.
[0047] Wherein, the foam stabilizer is composed of zinc cyanurate, simethicone, sodium lauryl sulfate, glyceryl tristearate and triethanolamine in a ratio of 1:2.6:0.5:0.2:0.95 by weight.
[0048] The foaming agent consists of dichloromethane, petroleum ether, sodium lauryl sulfate, and trichlorofluoromethane in parts by weight 1:0.56:1.2:0.92.
[0049] The catalyst is composed of dibutyltin diacetate and stannous benzoate in a ratio of 1:2 by mass.
[0050] Its production method comprises the following steps:
[0051] Step 1: Add polyether propylene glycol, poly...
Embodiment 3
[0057] A sponge for shoes, comprising the following raw materials in parts by weight: 53 parts of toluene diisocyanate, 45 parts of polyether propylene glycol, 35 parts of polyether glycerol, 3.2 parts of triethylenediamine, 2.4 parts of triethylamine, and 4.3 parts of foaming agent parts, 5.7 parts of foam stabilizer, 1.5 parts of catalyst, 6 parts of clam powder, 4 parts of sepiolite, and 2.5 parts of montmorillonite.
[0058] Wherein, the foam stabilizer is composed of zinc cyanurate, simethicone, sodium lauryl sulfate, glyceryl tristearate and triethanolamine in a ratio of 1:2.3:0.64:0.16:0.86 by weight.
[0059] The foaming agent consists of dichloromethane, petroleum ether, sodium lauryl sulfate, and trichlorofluoromethane in parts by weight 1:0.52:1.27:0.87.
[0060] The catalyst is composed of dibutyltin diacetate and stannous benzoate in a ratio of 1:1.5 in parts by mass.
[0061] Its production method comprises the following steps:
[0062] Step 1: Add polyether pr...
PUM
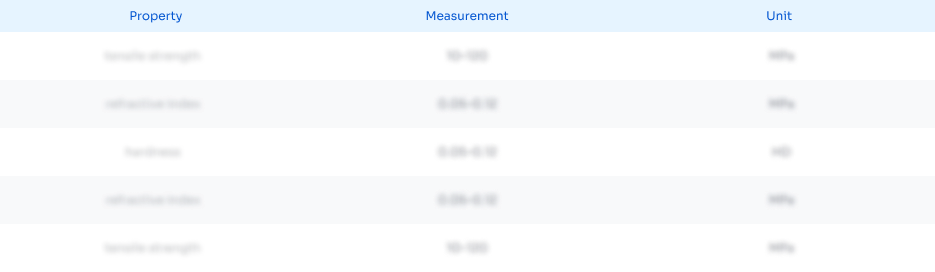
Abstract
Description
Claims
Application Information

- R&D
- Intellectual Property
- Life Sciences
- Materials
- Tech Scout
- Unparalleled Data Quality
- Higher Quality Content
- 60% Fewer Hallucinations
Browse by: Latest US Patents, China's latest patents, Technical Efficacy Thesaurus, Application Domain, Technology Topic, Popular Technical Reports.
© 2025 PatSnap. All rights reserved.Legal|Privacy policy|Modern Slavery Act Transparency Statement|Sitemap|About US| Contact US: help@patsnap.com