Mud contact point monitoring device in submarine pipeline laying process and monitoring method
A submarine pipeline and monitoring device technology, which is applied in pipeline laying and maintenance, pipe laying ships, mechanical equipment, etc., can solve the problems of easy damage of cables and low efficiency of information transmission, and achieve enhanced motion stability and good transmission effect Effect
- Summary
- Abstract
- Description
- Claims
- Application Information
AI Technical Summary
Problems solved by technology
Method used
Image
Examples
specific Embodiment approach 1
[0035] Specific implementation mode one: combine figure 1 and figure 2Describe this embodiment mode, a kind of mud contact point monitoring device in the subsea pipeline laying process of this embodiment mode, it comprises frame, traveling mechanism, monitoring mechanism, control mechanism, cable take-up mechanism and optical cable, and traveling mechanism comprises middle crawler mechanism and two The side crawler mechanism and the middle crawler mechanism are arranged on the upper part of the submarine pipeline along the length direction of the submarine pipeline. The middle crawler mechanism includes a middle support frame and a crawler transmission unit. The upper end of the frame is connected to the frame, and the two side crawler mechanisms are respectively arranged on the left and right sides of the submarine pipeline. The side crawler mechanism includes a side support frame and a crawler transmission unit. The frame is close to the side of the submarine pipeline, the...
specific Embodiment approach 2
[0038] Specific implementation mode two: combination figure 1 and figure 2 Describe this embodiment, the crawler belt drive unit of this embodiment comprises vehicle frame, drive wheel, guide wheel, crawler belt 2, magnet and crawler belt drive mechanism, drive wheel and guide wheel are respectively installed on the two ends of vehicle frame, and crawler belt 2 surrounds drive wheel Form crawler belt 2 transmission with the circumferential surface of guide wheel, magnet is installed on crawler belt 2, crawler belt driving mechanism is installed on the vehicle frame, and crawler belt driving mechanism is connected with driving wheel, realizes the rotation of driving wheel under the driving of crawler belt driving mechanism. With such arrangement, three crawlers 2 can be used to hold the submarine pipeline tightly, and each crawler is driven by an independent motor, so that the entire monitoring device can crawl along the submarine pipeline smoothly and flexibly. Magnets are a...
specific Embodiment approach 3
[0039] Specific implementation mode three: combination figure 1 and figure 2 Describe this embodiment, the crawler belt driving mechanism of this embodiment comprises motor, driving gear and driven gear, and motor is installed on the vehicle frame, and driving gear is installed on the output shaft of motor, and driven gear is installed on the axle of driving wheel, The driving gear meshes with the driven gear. So arranged, the motor output shaft rotates to drive the driving gear to rotate, the driving gear drives the driven gear to rotate, the driven gear drives the driving wheel of the crawler belt transmission unit to rotate, and the driving wheel drives the crawler belt 2 and the guide wheel to rotate. Other compositions and connections are the same as those in Embodiment 1 or Embodiment 2.
PUM
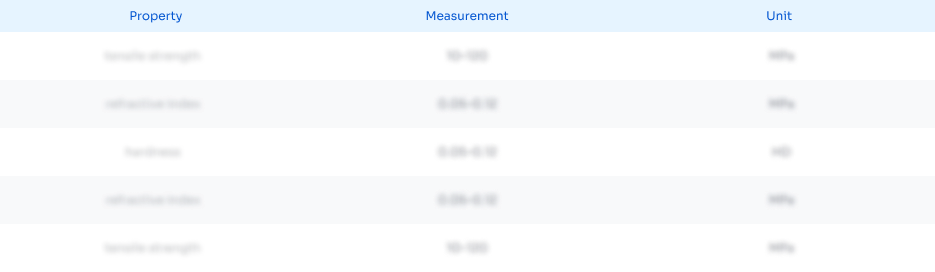
Abstract
Description
Claims
Application Information

- R&D
- Intellectual Property
- Life Sciences
- Materials
- Tech Scout
- Unparalleled Data Quality
- Higher Quality Content
- 60% Fewer Hallucinations
Browse by: Latest US Patents, China's latest patents, Technical Efficacy Thesaurus, Application Domain, Technology Topic, Popular Technical Reports.
© 2025 PatSnap. All rights reserved.Legal|Privacy policy|Modern Slavery Act Transparency Statement|Sitemap|About US| Contact US: help@patsnap.com