Wet treatment method for ferronickel and application thereof
A wet treatment, ferronickel technology, applied in the field of metallurgy, can solve the problems of slow reaction, long time, and inability to apply in large quantities, and achieve the effects of high leaching efficiency, avoiding environmental pollution, and accelerating the reaction rate
- Summary
- Abstract
- Description
- Claims
- Application Information
AI Technical Summary
Problems solved by technology
Method used
Image
Examples
Embodiment 1
[0027] Nickel iron wet treatment method, combination figure 1 The specific process is:
[0028] (1) Raw material pretreatment, nickel iron is crushed into powder or granules.
[0029] (2) a high pressure acid immersion, in a high pressure oxygen environment having a closed pressure of 6.5 MPa, a temperature of 90 ° C, the pulverized powder obtained by the step (1) is threatened by a concentration of 3 mol / L, and acetic acid is added to obtain a mixture The solid-liquid ratio of the mixed slurry is 1: 100 g / ml, the reaction time is 3 h;
[0030] (3) After the filtering process, the reaction is completed, and the filtrate and filter residue are filtered, and the nickel iron pulverization is added to the filtrate to carry out a small amount of copper from the liquid in the filtrate, and filter it again to obtain nickel Iron. Copper filtrate, nickel-iron returning to step (2), a high pressure acid immersion, circulating several times of cycling, a high copper content of nickel-iro...
Embodiment 2
[0036] A nickel iron wet treatment method, the specific process is:
[0037] (1) Pretreatment of raw materials, nickel iron is broken into powdered or granules of nickel iron.
[0038] (2) a high pressure acid immersion, in a high pressure oxygen environment having a closed pressure of 3.0 MPa, a temperature of 50 ° C, the pulverate obtained by the step (1) was immersed in a concentration of 8 mol / L, and acetylacetone was added. The mixed slurry, the solid-liquid ratio of the mixed slurry is 1: 200 g / ml, the reaction time is 1.5 h;
[0039] (3) After the filtering process, the reaction is completed, and the filtrate and filter residue are filtered, and the nickel iron pulverization is added to the filtrate to carry out a small amount of copper from the liquid in the filtrate, and filter it again to obtain nickel Iron. Copper filtrate, nickel-iron returning to step (2), a high pressure acid immersion, circulating several times of cycling, a high copper content of nickel-iron sl...
Embodiment 3
[0045] A nickel iron wet treatment method, the specific process is:
[0046] (1) Raw material pretreatment, nickel iron is broken into powder or granulated nickel iron.
[0047] (2) a high pressure acid immersion, in a high pressure oxygen environment having a closed pressure of 5.0 MPa, a temperature of 70 ° C, a deterioration of step (1) obtained by concentration of 5 mol / L, and an oxalic acid is added to give a mixture The slurry, the solid-liquid ratio of the mixed slurry is 1: 300 g / ml, the reaction time is 3 h;
[0048] (3) After the filtering process, the reaction is completed, and the filtrate and filter residue are filtered, and the nickel iron pulverization is added to the filtrate to carry out a small amount of copper from the liquid in the filtrate, and filter it again to obtain nickel Iron. Copper filtrate, nickel-iron returning to step (2), a high pressure acid immersion, circulating several times of cycling, a high copper content of nickel-iron slag, normal pres...
PUM
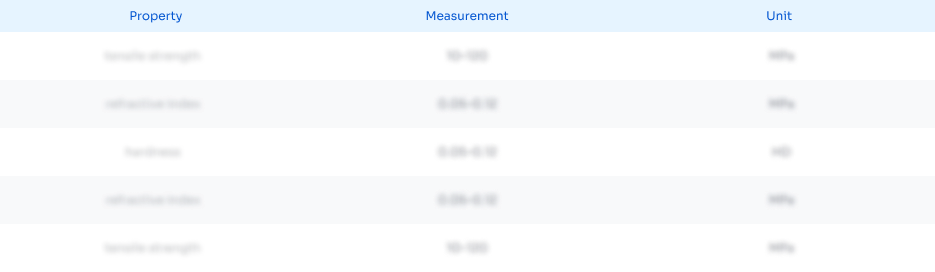
Abstract
Description
Claims
Application Information

- R&D Engineer
- R&D Manager
- IP Professional
- Industry Leading Data Capabilities
- Powerful AI technology
- Patent DNA Extraction
Browse by: Latest US Patents, China's latest patents, Technical Efficacy Thesaurus, Application Domain, Technology Topic, Popular Technical Reports.
© 2024 PatSnap. All rights reserved.Legal|Privacy policy|Modern Slavery Act Transparency Statement|Sitemap|About US| Contact US: help@patsnap.com