Method for synthesizing pyromellitic dianhydride through durene liquid-phase continuous oxygen-enriched precise oxidation
A technology of pyromellitic dianhydride and pyromellitic acid is applied in the field of synthesizing pyromellitic dianhydride by liquid-phase oxidation of pyromellitic tetratoluene, and can solve the problems of difficulty in product separation and purification, low reaction conversion rate and high reaction temperature problems, to achieve the effect of eliminating the need for recrystallization or sublimation purification process, high purity and efficient heat transfer
- Summary
- Abstract
- Description
- Claims
- Application Information
AI Technical Summary
Problems solved by technology
Method used
Image
Examples
Embodiment 1
[0022] The mixture of durene, acetic acid and cobalt-manganese-zinc-bromine catalyst (mass ratio 5:94.99:0.01) is continuously poured into the microchannel reactor, and the air is continuously introduced into the microchannel device at the same time as the liquid is injected, and the microchannel reaction The inner diameter of the microchannel is 10 µm.
[0023] The cobalt manganese zinc bromine catalyst is a mixture of cobalt acetate, manganese acetate, zinc acetate and tetrabromoethane, wherein the molar ratio of cobalt, manganese, zinc and bromine is 1:1:0.5:0.5.
[0024] Keep the temperature in the microchannel reactor at 180°C and the pressure in the reactor at 1.2 MPa. The pyromellitic acid is generated by the catalytic reaction between durene and oxygen, and the generated reaction solution rich in pyromellitic acid is discharged continuously. The content of tetracarboxylic acid is 98.5%.
[0025] Cool the pyromellitic acid reaction solution to 25°C to crystallize, ente...
Embodiment 2
[0027] The mixed solution of durene, acetic acid and cobalt-manganese-zinc-bromine catalyst (mass ratio 17:82.98:0.02) is continuously poured into the microchannel reactor, and oxygen-enriched gas, oxygen content of 30%, and the inner diameter of the microchannel of the microchannel reactor is 10µm.
[0028] The cobalt manganese zinc bromine catalyst is a mixture of cobalt acetate, manganese acetate, zinc acetate and tetrabromoethane, wherein the molar ratio of cobalt, manganese, zinc and bromine is 1:1:0.5:0.5.
[0029] Keep the temperature in the microchannel reactor at 260°C and the pressure in the reactor at 1.8 MPa. The pyromellitic acid is generated by the catalytic reaction between durene and oxygen, and the generated reaction solution rich in pyromellitic acid is discharged continuously. The content of tetracarboxylic acid is 98.6%.
[0030] Cool the pyromellitic acid reaction solution to 25°C to crystallize, enter the centrifuge for separation, remove acetic acid, wa...
Embodiment 3
[0032] The mixed solution of durene, acetic acid and cobalt-manganese-zinc-bromine catalyst (mass ratio 10:89.95:0.05) is continuously poured into the microchannel reactor, and oxygen-enriched gas, oxygen content of 50%, and the inner diameter of the microchannel of the microchannel reactor is 20µm.
[0033] The cobalt manganese zinc bromine catalyst is a mixture of cobalt acetate, manganese acetate, zinc acetate and tetrabromoethane, wherein the molar ratio of cobalt, manganese, zinc and bromine is 1:1:0.5:0.5.
[0034] Keep the temperature in the microchannel reactor at 220°C and the pressure in the reactor at 1.4 MPa. The pyromellitic acid is generated by the catalytic reaction between durene and oxygen, and the generated reaction liquid rich in pyromellitic acid is discharged continuously. The pyromellitic acid in the reaction liquid is The content of tetracarboxylic acid is 98.8%.
[0035] Cool the pyromellitic acid reaction solution to 25°C to crystallize, enter the cen...
PUM
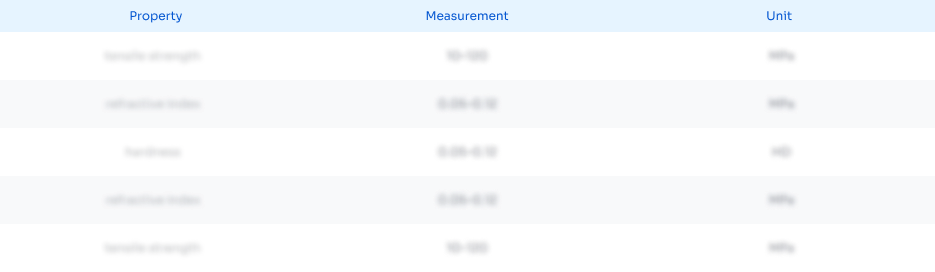
Abstract
Description
Claims
Application Information

- R&D Engineer
- R&D Manager
- IP Professional
- Industry Leading Data Capabilities
- Powerful AI technology
- Patent DNA Extraction
Browse by: Latest US Patents, China's latest patents, Technical Efficacy Thesaurus, Application Domain, Technology Topic, Popular Technical Reports.
© 2024 PatSnap. All rights reserved.Legal|Privacy policy|Modern Slavery Act Transparency Statement|Sitemap|About US| Contact US: help@patsnap.com