Self-heating assembly and production method
A self-heating and component technology, applied in heating devices, explosives, etc., can solve the problems of high oxygen dependence, high preparation cost, and low safety, and achieve low preparation cost, high heat conduction stability, and increased heating rate Effect
- Summary
- Abstract
- Description
- Claims
- Application Information
AI Technical Summary
Problems solved by technology
Method used
Image
Examples
preparation example Construction
[0078] According to one aspect of the present application, a method for preparing a self-heating component is provided, such as Figure 5 A flow chart showing a method for preparing a self-heating component according to an exemplary embodiment of the present application, such as Figure 5 It can be seen that the preparation process comprises the following steps:
[0079] In step S510, a fuel material portion is formed at the bottom of the casing;
[0080] In this embodiment, the fuel material part can be formed first, and then the fuel material part can be put into the casing; wherein, the fuel material part can be solidified and formed by pouring the pre-molding material of the fuel material part into a pre-customized mold. The application does not specifically limit this. Wherein, the fuel material portion may be provided with grooves with openings facing upwards, and the number of grooves may be, for example, 1, 2, 4, etc., which is not specifically limited in the present...
Embodiment 1
[0091](1) Under normal temperature conditions (20 DEG C), get 10g vegetable oil methyl ester, 30g magnesium powder, 25g calcium peroxide, 5g potassium sorbate and 10g polyurethane glue (this embodiment adopts the room temperature curable polyurethane glue that model is PU-201 Glue), added to a 500ml three-necked round-bottomed flask with stirring and vacuuming functions, and stirred for 5min;
[0092] (2) vacuumize, remove the air bubbles in the three-necked round-bottomed flask, close the stirring device, and make up the pressure in the bottle to normal pressure (0.1MPa) by air;
[0093] (3) Introduce the material in the bottle into a pre-customized mold, place it at room temperature for 30 minutes, realize solidification and molding, and obtain the fuel material part 3 with two upward grooves 120 (see figure 2 shown);
[0094] (4) Prepare the combustible protective layer 4 according to the size of the groove 120;
[0095] (5) According to the size of groove 120, prepare t...
Embodiment 2
[0099] Preparation method of self-heating component
[0100] (1) Under normal temperature conditions (20 ℃), get 10g methyl ester, 20g aluminum powder, 30g calcium peroxide, 2g sodium chloride, 3g potassium sorbate and 35g polyurethane glue (this embodiment adopts the model that can be PU-201 Polyurethane glue cured at room temperature), added to a 500ml three-necked round-bottomed flask with stirring and vacuuming functions, and stirred for 5 minutes;
[0101] Steps (2)~(4) are identical with embodiment 1;
[0102] (5) Prepare two ignition parts 2 according to the size of the groove 120; wherein, after mixing 0.5g of aluminum powder and 1g of potassium dichromate, put them into a single-layer non-woven bag to obtain two ignition parts 2, subsequently placed in the groove 120;
[0103] Steps (6)-(7) are the same as in Example 1.
PUM
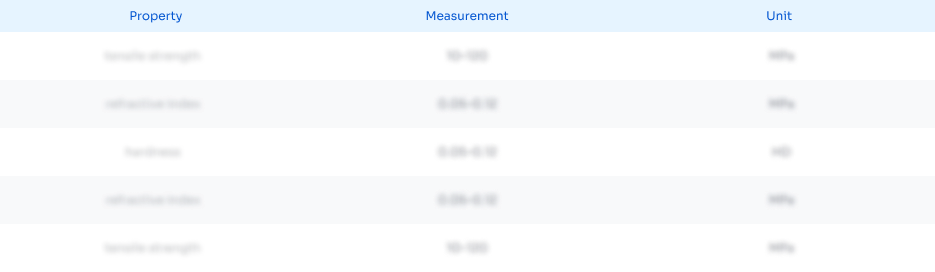
Abstract
Description
Claims
Application Information

- R&D
- Intellectual Property
- Life Sciences
- Materials
- Tech Scout
- Unparalleled Data Quality
- Higher Quality Content
- 60% Fewer Hallucinations
Browse by: Latest US Patents, China's latest patents, Technical Efficacy Thesaurus, Application Domain, Technology Topic, Popular Technical Reports.
© 2025 PatSnap. All rights reserved.Legal|Privacy policy|Modern Slavery Act Transparency Statement|Sitemap|About US| Contact US: help@patsnap.com