Flame-retardant nano cellulose containing phosphazene group, preparation method and flame-retardant polylactic acid of flame-retardant nano cellulose
A technology of nanocellulose and nitrile group, applied in the field of preparation, flame retardant nanocellulose, and flame retardant polylactic acid, can solve the problems of high raw material cost, low flame retardant efficiency, low thermal stability, etc., and reaches the initial decomposition temperature. High, high flame retardant efficiency, improve the effect of carbon formation rate and flame retardant performance
- Summary
- Abstract
- Description
- Claims
- Application Information
AI Technical Summary
Problems solved by technology
Method used
Image
Examples
Embodiment 1
[0032] Step (1): Add 9.40 g of phosphazene modifier to a mixture of 50 ml of water and 50 ml of absolute ethanol, and ultrasonicate at 10° C. for 30 minutes to obtain a hydrolyzed phosphazene modifier;
[0033] Step (2): Slowly add the hydrolyzed phosphazene modifier obtained in step (1) dropwise to the mixed solution of 9.40g cellulose nanofibers (CNF) and 90ml cyclohexane;
[0034] Step (3): after the dropwise addition, heat up to 40°C, and stir and reflux for 10 hours;
[0035] Step (4): The mixture obtained in step (3) is left to cool, and after the solid is completely precipitated, it is sucked and filtered, and vacuum-dried to obtain flame-retardant nanocellulose containing phosphazene groups;
[0036] Step (5): The above-mentioned flame-retardant nanocellulose and piperazine pyrophosphate (PPAP) are pre-mixed in a mass ratio of 1:10 to make a compound flame retardant, and then take 5 parts of the compound flame retardant and 95 Parts of polylactic acid were added to th...
Embodiment 2
[0039] Step (1): Add 44.5g of phosphazene modifier to a mixture of 10ml of water and 100ml of absolute ethanol, and ultrasonicate at 40°C for 5 minutes to obtain a hydrolyzed phosphazene modifier;
[0040] Step (2): Slowly add the hydrolyzed phosphazene modifier obtained in step (1) dropwise to the mixed solution of 8.9g cellulose nanocrystals (CNC) and 50ml toluene;
[0041] Step (3): After the dropwise addition, heat up to 20°C, and stir and reflux for 18 hours;
[0042] Step (4): The mixture obtained in step (3) is left to cool, and after the solid is completely precipitated, it is sucked and filtered, and vacuum-dried to obtain flame-retardant nanocellulose containing phosphazene groups;
[0043] Step (5): The above-mentioned flame-retardant nanocellulose and melamine polyphosphate (MPP) are pre-mixed in a mass ratio of 10:1 to make a compound flame retardant, and then take 20 parts of the compound flame retardant and 80 Parts of polylactic acid were added to the torque r...
Embodiment 3
[0046] Step (1): Add 20.5 g of phosphazene modifier into a mixture of 15 ml of water and 75 ml of absolute ethanol, and ultrasonicate at 20° C. for 15 minutes to obtain a hydrolyzed phosphazene modifier;
[0047] Step (2): Slowly add the hydrolyzed phosphazene modifier obtained in step (1) dropwise to the mixed solution of 8.2g cellulose nanocrystals (CNC) and 100ml absolute ethanol;
[0048] Step (3): after the dropwise addition, heat up to 80°C, and stir and reflux for 12 hours;
[0049]Step (4): The mixture obtained in step (7) is left to cool, and after the solid is completely precipitated, it is suction filtered and vacuum-dried to obtain flame-retardant nanocellulose (M-CNC) containing phosphazene groups;
[0050] Step (5): Pre-mix M-CNC and ammonium polyphosphate (APP) at a mass ratio of 3:7 to make a compound flame retardant, then take 10 parts of the compound flame retardant and 90 parts of polylactic acid together Add to the torque rheometer, melt blending at 180 ° ...
PUM
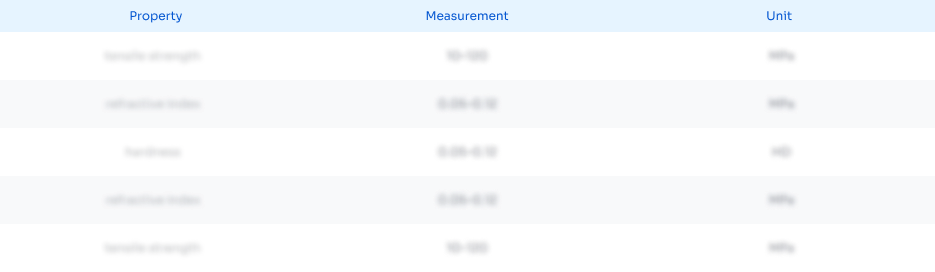
Abstract
Description
Claims
Application Information

- Generate Ideas
- Intellectual Property
- Life Sciences
- Materials
- Tech Scout
- Unparalleled Data Quality
- Higher Quality Content
- 60% Fewer Hallucinations
Browse by: Latest US Patents, China's latest patents, Technical Efficacy Thesaurus, Application Domain, Technology Topic, Popular Technical Reports.
© 2025 PatSnap. All rights reserved.Legal|Privacy policy|Modern Slavery Act Transparency Statement|Sitemap|About US| Contact US: help@patsnap.com