Method for preparing 3-nitro-4-chlorobenzotrifluoride through continuous adiabatic nitration and micro-reaction equipment
A chlorobenzotrifluorotoluene and adiabatic nitration technology, which is applied in the preparation of nitro compounds, chemical instruments and methods, and the preparation of organic compounds, etc., can solve the problem of the reduction of nitration reaction rate, the restriction of industrial production of micro-reaction systems, and the reduction of reaction conversion rate, etc. problems, to achieve the effects of comprehensive cost reduction, safe production process, and short response time
- Summary
- Abstract
- Description
- Claims
- Application Information
AI Technical Summary
Problems solved by technology
Method used
Image
Examples
Embodiment 1
[0042] (1) under stirring state, add concentrated sulfuric acid (mass fraction is 98%) in concentrated nitric acid and cool reaction solution, obtain mixed acid material, the mass ratio of concentrated sulfuric acid and concentrated nitric acid is 8:1;
[0043] (2) In a constant temperature oil bath, the mixed acid material and p-chlorobenzotrifluoride are preheated to 70°C respectively (the flow rates of the mixed acid and chlorobenzene plunger pumps are respectively 160ml / min and 30ml / min), and they are continuously transported to In the micro-reaction system, according to the reaction molar ratio of nitric acid and chlorobenzene is 1.08:1; first enter the micro-sieve reactor for adiabatic nitration reaction, the outlet temperature of the micro-sieve reactor is 130 ° C, and then continuously flow through the static mixing A device and a reaction delay tube are used to carry out a continuous nitration reaction, and the residence time of the reaction solution in the micro-react...
Embodiment 2
[0046] (1) under stirring state, add concentrated sulfuric acid (mass fraction is 98%) in concentrated nitric acid and cool reaction solution, obtain mixed acid material, the mass ratio of concentrated sulfuric acid and concentrated nitric acid is 10:1;
[0047](2) In a constant temperature oil bath, the mixed acid material and p-chlorobenzotrifluoride are preheated to 80°C respectively (the flow rates of the mixed acid and chlorobenzene plunger pumps are respectively 160ml / min and 30ml / min), and they are continuously transported to In the micro-reaction system, according to the reaction molar ratio of nitric acid and chlorobenzene is 1.05:1; first enter the micro-sieve reactor for adiabatic nitration reaction, the outlet temperature of the micro-sieve reactor is 140 ° C, and then continuously flow through static mixing A device and a reaction delay tube are used to carry out a continuous nitration reaction, and the residence time of the reaction solution in the micro-reaction ...
Embodiment 3
[0050] (1) under stirring state, add concentrated sulfuric acid (mass fraction is 98%) in concentrated nitric acid and cool reaction solution, obtain mixed acid material, the mass ratio of concentrated sulfuric acid and concentrated nitric acid is 12:1;
[0051] (2) In a constant temperature oil bath, the mixed acid material and p-chlorobenzotrifluoride are preheated to 75°C respectively (the flow rates of the mixed acid and chlorobenzene plunger pumps are respectively 160ml / min and 30ml / min), and they are continuously transported to In the micro-reaction system, according to the reaction molar ratio of nitric acid and chlorobenzene is 1.15:1; first enter the micro-sieve reactor for adiabatic nitration reaction, the outlet temperature of the micro-sieve reactor is 135 ° C, and then continuously flow through static mixing A device and a reaction delay tube are used to carry out a continuous nitration reaction, and the residence time of the reaction solution in the micro-reaction...
PUM
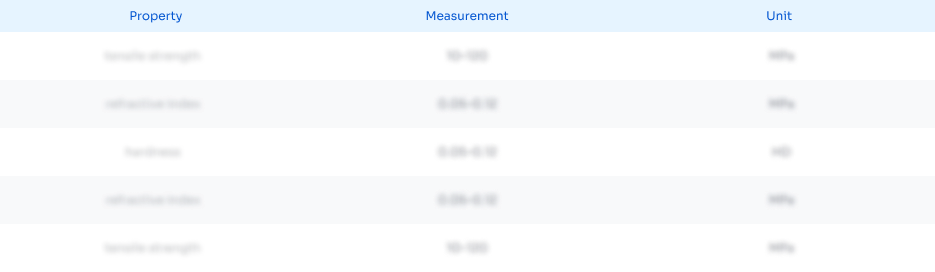
Abstract
Description
Claims
Application Information

- R&D Engineer
- R&D Manager
- IP Professional
- Industry Leading Data Capabilities
- Powerful AI technology
- Patent DNA Extraction
Browse by: Latest US Patents, China's latest patents, Technical Efficacy Thesaurus, Application Domain, Technology Topic, Popular Technical Reports.
© 2024 PatSnap. All rights reserved.Legal|Privacy policy|Modern Slavery Act Transparency Statement|Sitemap|About US| Contact US: help@patsnap.com