Multi-degree-of-freedom wind power tower boarding trestle
A technology of wind power towers and degrees of freedom, applied in the direction of floating bridges, bridges, bridge forms, etc., can solve the problems of low boarding efficiency, high cost, weight and large occupied space, and achieve high boarding efficiency, low cost, and light weight Effect
- Summary
- Abstract
- Description
- Claims
- Application Information
AI Technical Summary
Problems solved by technology
Method used
Image
Examples
Embodiment Construction
[0020] The present invention will be described in further detail below in conjunction with the embodiments and accompanying drawings.
[0021] Such as figure 1 , 2 As shown, a multi-degree-of-freedom wind power tower boarding trestle includes a support base 2 and a hydraulic pump station 5 installed on the bow deck 1, and an attitude sensor 3 is installed at the bottom center of the support base 2. The upper end of the machine base 2 is connected to the azimuth turntable 6 through the roll mechanism 4, and the azimuth turntable 6 is connected to the lower ramp 9 through the pitch mechanism 7. An upper ramp 10 is movable in the lower ramp 9, and a wind power tower is installed at one end of the upper ramp 10. The ship berth column 11, the wind power tower is installed on the ship berth column 11 with a wind power tower ladder 12, the bottom of the upper ramp 10 is connected with the bottom of the lower ramp 9 through the telescopic mechanism 8; the roll mechanism 4 includes a ...
PUM
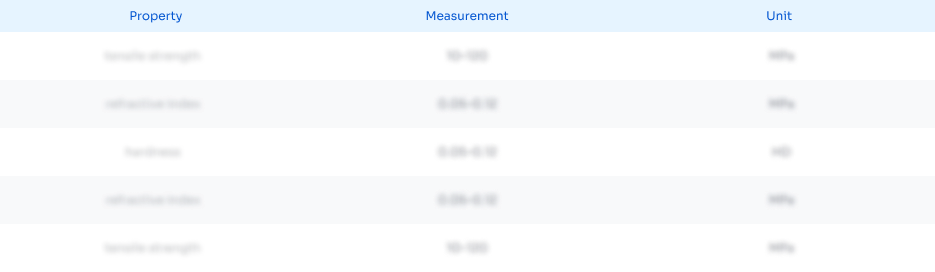
Abstract
Description
Claims
Application Information

- R&D Engineer
- R&D Manager
- IP Professional
- Industry Leading Data Capabilities
- Powerful AI technology
- Patent DNA Extraction
Browse by: Latest US Patents, China's latest patents, Technical Efficacy Thesaurus, Application Domain, Technology Topic, Popular Technical Reports.
© 2024 PatSnap. All rights reserved.Legal|Privacy policy|Modern Slavery Act Transparency Statement|Sitemap|About US| Contact US: help@patsnap.com