Glazed tile surface treatment method and application
A technology of surface treatment and glazed tiles, applied in the field of ceramic technology, can solve the problems of complex preparation process, low hardness, poor wear resistance, etc., and achieve the effect of increasing ion exchange rate, enhancing wear resistance, and enhancing wear resistance
- Summary
- Abstract
- Description
- Claims
- Application Information
AI Technical Summary
Problems solved by technology
Method used
Examples
Embodiment 1
[0031] A surface treatment method for glazed tiles, comprising the following steps:
[0032] S1. First, take raw material potassium salt, adsorbent and activator to mix, the weight percent of described raw material is: potassium salt 95%, adsorbent 1.5%, activator 3.5%, described potassium salt is KNO 3 , KCl, K 2 SO 4 Three mixed salt, and KNO 3 , KCl, K 2 SO 4 The mass ratio of 63:22:15, the adsorbent is Al 2 O 3 , the activator is Sb 2 O 3 Then, the above-mentioned raw materials are put into the aluminum salt tank and mixed evenly, and heated to 450 ℃ to be melted to obtain a molten salt mixture;
[0033] S2. The glazed tile is immersed in the molten salt mixture for treatment and taken out, immersed at 450° C. for 8 hours, taken out, cooled to room temperature, and the surface cleaned to obtain a surface-treated glazed tile.
Embodiment 2
[0034] Example 2 (lower processing temperature relative to Example 1)
[0035] A surface treatment method for glazed tiles, comprising the following steps:
[0036] S1. First, take raw material potassium salt, adsorbent and activator to mix, the weight percent of described raw material is: potassium salt 95%, adsorbent 1.5%, activator 3.5%, described potassium salt is KNO 3 , KCl, K 2 SO 4 Three mixed salt, and KNO 3 , KCl, K 2 SO 4 The mass ratio of 63:22:15, the adsorbent is Al 2 O 3 , the activator is Sb 2 O 3 Then, the above-mentioned raw materials are put into the aluminum salt tank and mixed evenly, and heated to 400 ℃ to be melted to obtain a molten salt mixture;
[0037] S2. The glazed tile is immersed in the molten salt mixture for treatment and taken out, immersed at 400° C. for 8 hours, taken out, cooled to room temperature, and cleaned to obtain a surface-treated glazed tile.
Embodiment 3
[0038] Example 3 (higher processing temperature relative to Example 1)
[0039] A surface treatment method for glazed tiles, comprising the following steps:
[0040] S1. First, take raw material potassium salt, adsorbent and activator to mix, the weight percent of described raw material is: potassium salt 95%, adsorbent 1.5%, activator 3.5%, described potassium salt is KNO 3 , KCl, K 2 SO 4 Three mixed salt, and KNO 3 , KCl, K 2 SO 4 The mass ratio of 63:22:15, the adsorbent is Al 2 O 3 , the activator is Sb 2 O 3 Then, the above-mentioned raw materials are put into the aluminum salt tank and mixed evenly, and heated to 400 ℃ to be melted to obtain a molten salt mixture;
[0041] S2. The glazed tile is immersed in the molten salt mixture for treatment and then taken out, immersed at 480° C. for 8 hours, taken out, cooled to room temperature, and the surface is cleaned to obtain a surface-treated glazed tile.
PUM
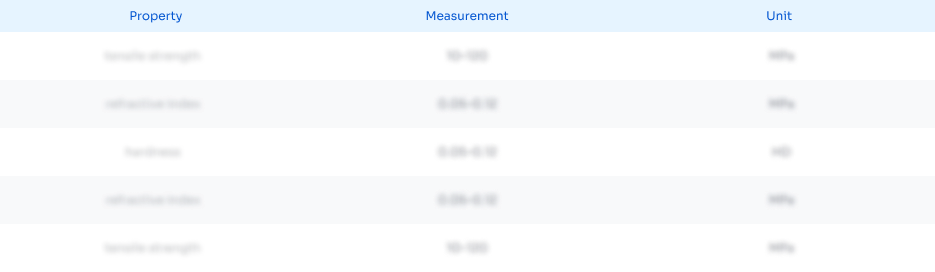
Abstract
Description
Claims
Application Information

- R&D
- Intellectual Property
- Life Sciences
- Materials
- Tech Scout
- Unparalleled Data Quality
- Higher Quality Content
- 60% Fewer Hallucinations
Browse by: Latest US Patents, China's latest patents, Technical Efficacy Thesaurus, Application Domain, Technology Topic, Popular Technical Reports.
© 2025 PatSnap. All rights reserved.Legal|Privacy policy|Modern Slavery Act Transparency Statement|Sitemap|About US| Contact US: help@patsnap.com