Method for reducing residue output in sodium hydrosulfite production process
A production process, sodium hydrosulfite technology, applied in chemical instruments and methods, preparation of organic compounds, separation/purification of carboxylic acid compounds, etc., can solve problems such as excessive residues and ecological environment damage, speed up the recovery rate and reduce raw materials Consumption and energy saving effects
- Summary
- Abstract
- Description
- Claims
- Application Information
AI Technical Summary
Problems solved by technology
Method used
Image
Examples
Embodiment 1
[0027] The invention provides a method for reducing the amount of residue generated in the production process of hydrosulfite, comprising the following steps:
[0028] S1. Put the distilled hydrosulfite residue into the first-effect evaporator and heat it with steam. After evaporation, put it into the second-effect evaporator for concentration to obtain the concentrate and condensate; the concentrate is 400-500g / L, and the condensate is condensed through waste water into the waste water tank.
[0029] S2. After the concentrated solution is sent to the solidified B kettle, it is heated and concentrated with steam. The concentrated solution in the solidified B kettle is concentrated to the standard and then discharged to the centrifuge head tank, and then sent to a centrifuge for centrifugation to obtain sodium formate and centrifuged mother liquor;
[0030] The gas generated by the two-effect evaporator and the curing B kettle passes through the circulating water condenser, the...
Embodiment 2
[0034] The invention provides a method for reducing the amount of residue generated in the production process of hydrosulfite, comprising the following steps:
[0035] S1. Put the distilled hydrosulfite residue into the first-effect evaporator and heat it with steam. After evaporation, put it into the second-effect evaporator for concentration to obtain the concentrate and condensate; the concentrate is 400-500g / L, and the condensate is condensed through waste water into the waste water tank.
[0036] S2. After the concentrated solution is sent to the solidified B kettle, it is heated and concentrated with steam. The concentrated solution in the solidified B kettle is concentrated to the standard and then discharged to the centrifuge head tank, and then sent to a centrifuge for centrifugation to obtain sodium formate and centrifuged mother liquor;
[0037] The gas generated by the two-effect evaporator and the curing B kettle passes through the circulating water condenser, the...
Embodiment 3
[0042] The invention provides a method for reducing the amount of residue generated in the production process of hydrosulfite, comprising the following steps:
[0043] S1. Put the distilled hydrosulfite residue into the first-effect evaporator and heat it with steam. After evaporation, put it into the second-effect evaporator for concentration to obtain the concentrate and condensate; the concentrate is 400-500g / L, and the condensate is condensed through waste water into the waste water tank.
[0044] S2. After the concentrated solution is sent to the solidified B kettle, it is heated and concentrated with steam. The concentrated solution in the solidified B kettle is concentrated to the standard and then discharged to the centrifuge head tank, and then sent to a centrifuge for centrifugation to obtain sodium formate and centrifuged mother liquor;
[0045] The gas generated by the two-effect evaporator and the curing B kettle passes through the circulating water condenser, the...
PUM
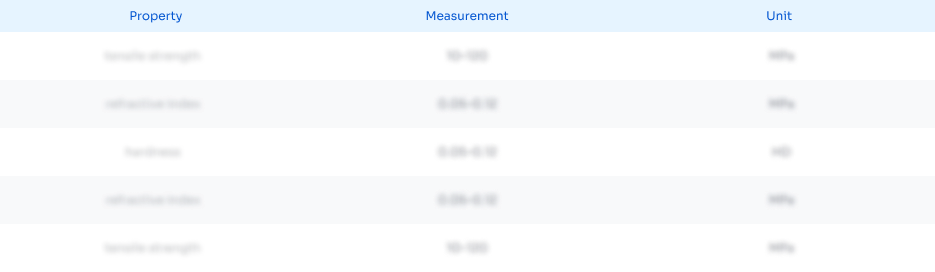
Abstract
Description
Claims
Application Information

- R&D Engineer
- R&D Manager
- IP Professional
- Industry Leading Data Capabilities
- Powerful AI technology
- Patent DNA Extraction
Browse by: Latest US Patents, China's latest patents, Technical Efficacy Thesaurus, Application Domain, Technology Topic, Popular Technical Reports.
© 2024 PatSnap. All rights reserved.Legal|Privacy policy|Modern Slavery Act Transparency Statement|Sitemap|About US| Contact US: help@patsnap.com