A cooling-to-energy aerospace engine
An engine and energy technology, applied in engine components, machine/engine, engine cooling, etc., can solve the problem that it is difficult for the engine to greatly increase the working temperature of the nozzle in the energy chamber, it is difficult to ensure the structure and material strength of the engine, and it is impossible to use high-energy working fluid To achieve the effect of reducing the difficulty of structure and manipulation, simple and easy storage and addition, and ensuring the structure and material strength
- Summary
- Abstract
- Description
- Claims
- Application Information
AI Technical Summary
Problems solved by technology
Method used
Image
Examples
Embodiment Construction
[0020] Such as figure 1 Shown: be the structural representation of embodiment 1 of the present invention, a kind of cooling transfer energy aerospace engine, its energy chamber (combustion chamber) 1, has the aperture 2 of uniform distribution, the aperture 2 other ends and working fluid conduit (propulsion) agent) 6 in communication, the working fluid conduit 6 is in communication with the working fluid compression regulator 8 and the working fluid constant temperature storage tank 7 (including the liquid oxygen storage tank 7-1); the energy chamber (combustion chamber) 1 is in communication with the inner nozzle 4, and the inner The corresponding inner nozzle 5 of nozzle pipe 4 ejects energy to do work; Ignition or energy launching device 3 is installed in the energy chamber (combustion chamber) 1, just an ignition device; the outer wall of energy chamber (combustion chamber) 1 and the inner nozzle pipe 4 The outer wall has a temperature detector 9 connected to the thermosta...
PUM
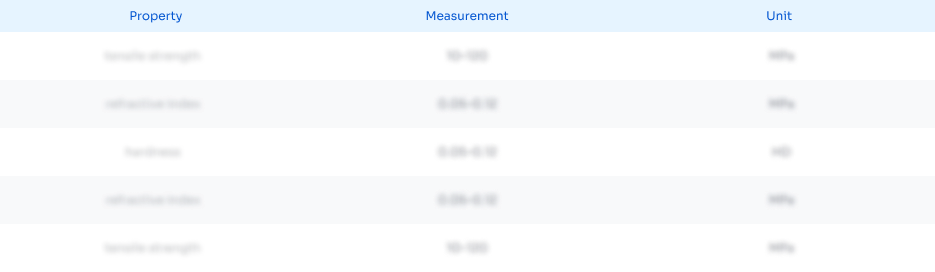
Abstract
Description
Claims
Application Information

- Generate Ideas
- Intellectual Property
- Life Sciences
- Materials
- Tech Scout
- Unparalleled Data Quality
- Higher Quality Content
- 60% Fewer Hallucinations
Browse by: Latest US Patents, China's latest patents, Technical Efficacy Thesaurus, Application Domain, Technology Topic, Popular Technical Reports.
© 2025 PatSnap. All rights reserved.Legal|Privacy policy|Modern Slavery Act Transparency Statement|Sitemap|About US| Contact US: help@patsnap.com