Manufacturing and forming process for oil pump rotor
A molding process and oil pump technology, applied in the direction of manufacturing tools, metal processing equipment, sawing machine accessories, etc., can solve the problems of reducing the production efficiency of the outer rotor of the oil pump, reducing the cutting quality, and polluting the working environment, so as to prevent pollution of the working environment , improve cutting quality and improve efficiency
- Summary
- Abstract
- Description
- Claims
- Application Information
AI Technical Summary
Problems solved by technology
Method used
Image
Examples
Embodiment Construction
[0038] Embodiments of the present invention will be described below with reference to the drawings. In the process, in order to ensure the clarity and convenience of illustration, we may exaggerate the width of the lines or the size of the constituent elements in the diagram.
[0039] In addition, the following terms are defined based on the functions in the present invention, and may be different according to the user's or operator's intention or practice. Therefore, these terms are defined based on the entire content of this specification.
[0040] Such as Figure 1 to Figure 9 As shown, an oil pump rotor manufacturing and molding process uses a kind of oil pump rotor manufacturing and molding equipment. The oil pump rotor manufacturing and molding equipment includes a bottom plate 1, a support device 2 and a cutting device 3. The specific method of processing the rotor embryo body is as follows:
[0041] S1. Feeding process: manually place the outer rotor body of the oil...
PUM
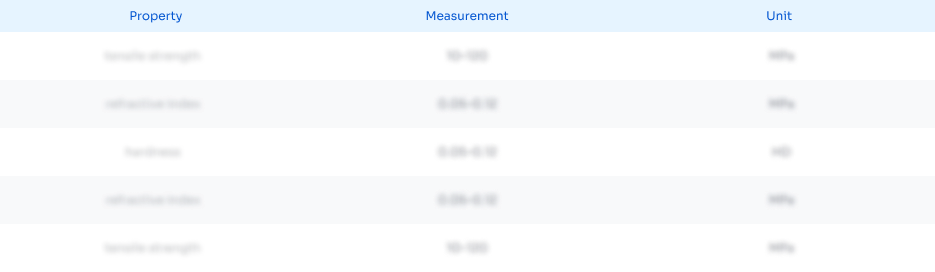
Abstract
Description
Claims
Application Information

- Generate Ideas
- Intellectual Property
- Life Sciences
- Materials
- Tech Scout
- Unparalleled Data Quality
- Higher Quality Content
- 60% Fewer Hallucinations
Browse by: Latest US Patents, China's latest patents, Technical Efficacy Thesaurus, Application Domain, Technology Topic, Popular Technical Reports.
© 2025 PatSnap. All rights reserved.Legal|Privacy policy|Modern Slavery Act Transparency Statement|Sitemap|About US| Contact US: help@patsnap.com