Built-in permanent magnet synchronous motor sensorless parameter error compensation strategy
A permanent magnet synchronous motor and sensor parameter technology, which is applied in the control of generators, motor control, motor generator control, etc., can solve the problems that are easily affected by flux linkage, inductance parameter changes and system delay, and achieve robustness The effect of improving and improving the accuracy of position estimation
- Summary
- Abstract
- Description
- Claims
- Application Information
AI Technical Summary
Problems solved by technology
Method used
Image
Examples
Embodiment Construction
[0060] The present invention will be described in detail below in conjunction with the accompanying drawings and specific embodiments.
[0061] A parameter error compensation strategy for a built-in permanent magnet synchronous motor without a position sensor according to the present invention is specifically implemented according to the following steps:
[0062] Step 1, based on the indirect calculation method of flux linkage, estimate the MT shaft current and replace the estimated value with a given flux linkage, so as to improve the rotor position estimation based on flux linkage, the principle block diagram is as follows figure 1 As shown, the specific steps are as follows:
[0063] Step 1.1, for the three-phase current i A i B i C Sampling is performed, and Clarke transformation is performed on it to obtain the α-axis and β-axis currents, and then the estimated value of the stator flux linkage angle is calculated and the electromagnetic torque estimate As shown in ...
PUM
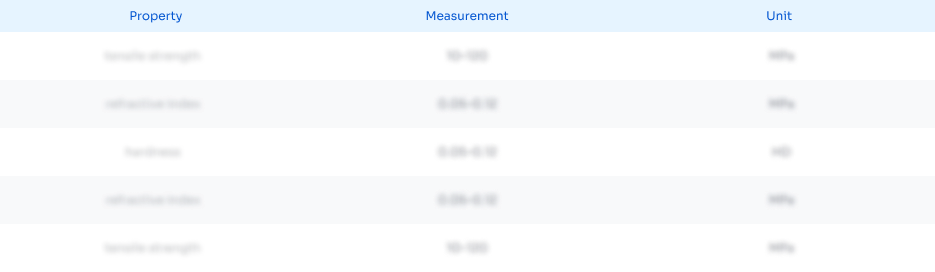
Abstract
Description
Claims
Application Information

- R&D
- Intellectual Property
- Life Sciences
- Materials
- Tech Scout
- Unparalleled Data Quality
- Higher Quality Content
- 60% Fewer Hallucinations
Browse by: Latest US Patents, China's latest patents, Technical Efficacy Thesaurus, Application Domain, Technology Topic, Popular Technical Reports.
© 2025 PatSnap. All rights reserved.Legal|Privacy policy|Modern Slavery Act Transparency Statement|Sitemap|About US| Contact US: help@patsnap.com