Method for preventing or reducing coking of inner wall of ascension pipe of coke oven
A tube inner wall and coke oven technology, which is applied in the fields of coal coking, energy conservation and environmental protection, to achieve the effects of reducing coking, ensuring heat exchange efficiency, and increasing production
- Summary
- Abstract
- Description
- Claims
- Application Information
AI Technical Summary
Problems solved by technology
Method used
Image
Examples
Embodiment 1
[0046] Such as figure 1 , figure 2 As shown, in this embodiment, in order to prevent or eliminate coking on the inner wall of the riser, an inclined inert gas inlet pipe 4 is arranged on the side of the upper end of the riser 2, and the high-pressure inert gas is passed from the upper end of the riser 2 to the inner wall of the riser. The tangential direction of 5 is supplied into the riser 2, so that the high-pressure inert gas forms a continuous airflow in the riser 2 along the inner wall 5 of the riser and moves downward at a high speed. Viscous components such as tar and the like precipitated by contact with the pipe inner wall 5 (externally installed riser waste heat recovery device 3) are removed.
[0047] In this embodiment, the pressure of the high-pressure inert gas is 0.2 MPa, which can ensure that the high-pressure inert gas forms sufficient scouring force on the inner wall 5 of the riser tube to effectively remove related viscous substances.
[0048] In this emb...
Embodiment 2
[0054] Such as image 3 As shown, in this embodiment, the inert gas inlet pipe 4 is movably connected with the riser pipe 2, and the angle between its axis and the horizontal plane can be adjusted as required, or continuously reciprocated between 0° and 30° to ensure high-pressure inertness. The gas covers the entire riser inner wall 5 in the raw gas flow area.
[0055] In this embodiment, the high-pressure inert gas is fed continuously. Through the continuous feeding method, an airflow barrier is formed on the inner wall 5 of the riser, which can prevent viscous substances such as tar in the raw gas from directly contacting the inner wall 5 of the riser, and eliminate the phenomenon of coking on the inner wall 5 of the riser.
[0056] In this embodiment, the high-pressure inert gas is the high-pressure superheated steam produced by the CDQ waste heat boiler. On the one hand, due to the high temperature of the superheated steam, the adhesion and precipitation of tar will be e...
Embodiment 3
[0058] In this embodiment, on the basis of Embodiment 1, in order to ensure that the flow area of the high-pressure inert gas on the inner wall 5 of the riser covers all the inner wall 5 of the riser, a plurality of inert gas inlet pipes 4 arranged side by side vertically (such as Figure 4 shown).
[0059] In this embodiment, the high-pressure inert gas adopts pressurized high-pressure CO 2 The gas, on the one hand, utilizes the high-pressure air flow to flush the tar deposited on the inner wall 5 of the riser to prevent the newly precipitated tar from depositing on the inner wall 5 of the riser; 1 The carbon dissolution reaction occurs in a high-temperature environment, and the CO 2 Oxidation into CO not only increases the output of coke oven gas, but also absorbs CO produced by other systems, devices or processes to a certain extent. 2 role to achieve CO 2 The transformation of resources into resources plays a positive role in promoting carbon emission reduction in the...
PUM
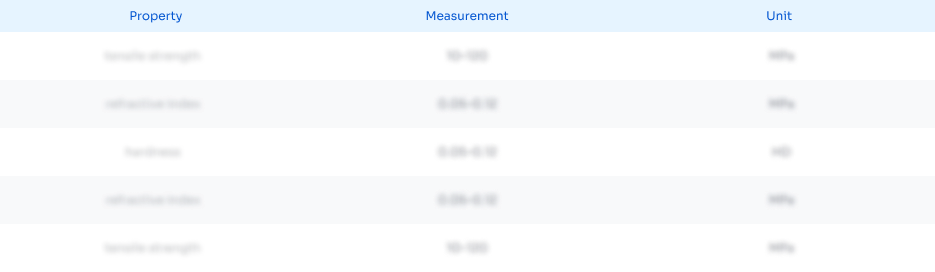
Abstract
Description
Claims
Application Information

- R&D Engineer
- R&D Manager
- IP Professional
- Industry Leading Data Capabilities
- Powerful AI technology
- Patent DNA Extraction
Browse by: Latest US Patents, China's latest patents, Technical Efficacy Thesaurus, Application Domain, Technology Topic, Popular Technical Reports.
© 2024 PatSnap. All rights reserved.Legal|Privacy policy|Modern Slavery Act Transparency Statement|Sitemap|About US| Contact US: help@patsnap.com